Da oltre 50 anni GGS Footwear Moulds crea stampi per il settore calzaturiero, unendo l’artigianalità del Made in Italy alla tecnologia più avanzata. il risultato è un prodotto di alta qualità, affidabile e durevole
Da piccola impresa artigianale fondata nel 1970 dall’imprenditore Lino Gobbato, GGS Footwear Moulds è oggi un’importante realtà internazionale specializzata nella produzione di stampi per il settore calzaturiero in grado di soddisfare ogni esigenza di personalizzazione. Mattia Gobbato, terza generazione dell’azienda di Legnaro, in provincia di Padova, ci illustra il caso di successo, frutto di un mix equilibrato tra esperienza tradizionale e innovazione tecnologica.
Mattia Gobbato, come nasce l’azienda?
“GGS nasce negli anni Settanta per volontà di mio nonno, Lino Gobbato, il quale, dopo una precedente esperienza come responsabile di settore, decide di mettersi in proprio fondando un’impresa specializzata nella realizzazione di stampi per la produzione di stivali in PVC. La dedizione e l’ambizione che lo hanno sempre contraddistinto sono state trasmesse ai suoi figli, ancora oggi al timone dell’azienda di famiglia: Roberto e Franco Gobbato. Grazie a un grande e continuo lavoro di squadra, oggi l’azienda è in grado di soddisfare ogni esigenza produttiva, realizzando stampi per tutte le macchine a iniezione esistenti sul mercato mondiale. I nostri prodotti sono composti da alluminio di alta qualità, che consente l’iniezione in modo perfetto di qualsiasi materiale utilizzato nel comparto calzaturiero (PVC, EVA, PU, TPU, gomme naturali, gomme termoplastiche ecc.). Offriamo diverse tipologie di stampi: monocolore, bicolore, tricolore e con inserti. Inoltre, assistiamo puntualmente il cliente nella scelta delle finiture, dal laser alla fotoincisione, dalla lucidatura alla sabbiatura”.
Quando siete passati allo stampaggio del poliuretano e perché?
“I primi disegni risalgono alla fine degli anni Novanta. Il poliuretano è molto più leggero rispetto al PVC, fornisce un isolamento termico maggiore alle basse temperature e vanta migliorie a livello tecnico e di comfort per chi è costretto per esempio a utilizzare calzature safety per tante ore al giorno”.
Lavorate con grandi aziende in tutto il mondo. La vostra vocazione internazionale è da subito innegabile.
“All’inizio fabbricavamo stampi per stivali in PVC destinati al governo della Germania dell’Est. Siamo sempre proiettati verso nuovi traguardi in Europa, Russia, Stati Uniti, Canada e Sud America, Africa, Giappone, Australia e Nuova Zelanda. A oggi il 90% del fatturato lo dobbiamo ai nostri rapporti con l’estero”.
Qual è il vostro livello di produttività?
“Abbiamo sempre fatto leva sui grandi volumi. Negli anni sono state introdotte otto macchine CNC robotizzate a cinque assi, palettizzate, che lavorano H24 per 365 giorni all’anno. Non ci esimiamo dal lavorare il sabato e la domenica. Abbiamo strutturato l’azienda affinché sia produttiva anche di notte senza personale con un sistema di e-mail alert che ci consente di intervenire in caso di eventuali malfunzionamenti”.
E la vostra carta vincente?
“Gestiamo internamente l’intero ciclo di produzione, affiancando il cliente dalla fase creativa fino al collaudo. Partendo dal concetto iniziale eseguiamo il progetto in 2D per chiarire tutti i dati tecnici relativi allo stampo. Una volta confermato il disegno realizziamo il modello in 3D e in seguito creiamo la maquette tramite la prototipazione con la stampante 3D. Diamo così una forma concreta all’idea del cliente e mettiamo a punto il design e i dettagli del modello in ogni particolare. A seguito dell’approvazione del progetto procediamo con la produzione dello stampo, utilizzando software all’avanguardia e macchine CNC robotizzate a 5 assi ad alta velocità. Grazie anche al reverse engineering con tecnologie di misurazione 3D siamo in grado di potenziare il controllo qualità e ottimizzare i tempi di lavorazione. Abbiamo instaurato una collaborazione proficua basata sul rispetto della segretezza con le maggiori aziende costruttrici di macchine a iniezione per risolvere qualsiasi problema del cliente, aiutandolo nella realizzazione di un prodotto finale migliore. Ogni volta che partiamo con un nuovo progetto, cerchiamo di portare il cliente al successo tramite la collaborazione stretta con tutti gli stakeholder, da noi stampisti al produttore di macchine a iniezione, fino a quello di materie plastiche e di coloranti. Credo molto nella necessità di fornire al cliente un servizio a 360 gradi che lo faccia sentire protetto e supportato, affinché sia pronto per entrare in produzione quanto prima. Del resto stiamo parlando di stampi e macchinari che richiedono investimenti anche pari a sei zeri”.
Come ha costruito il suo ruolo in GGS?
“Classe 1988, dopo aver studiato informatica sono entrato in azienda a 18 anni partendo dalle basi. Per 12 anni mi sono occupato via via di progettazione 2D e 3D, reverse engineering, fresatura, programmazione CNC e CAM 3D dopodiché, forte della competenza trasversale acquisita, ho colto l’opportunità di passare al settore commerciale. Ho sviluppato l’attitudine al problem solving nel customer care. Mi piace viaggiare e viaggio molto, e quando arrivo dal cliente non vesto solo i panni del venditore, ma intervengo nella risoluzione dei problemi, grazie anche alla possibilità di interfacciarmi con il nostro team, ma soprattutto con mio padre e mio zio, forti di 53 anni di storia aziendale alle spalle. Un servizio, questo, molto apprezzato. La GGS è un’azienda in continua evoluzione che partecipa attivamente ai nuovi progetti e allo sviluppo delle ultime tecnologie nel mondo calzaturiero. Progetti e tecnologie che, una volta perfezionati, vengono puntualmente condivisi con i nostri fedeli clienti”.
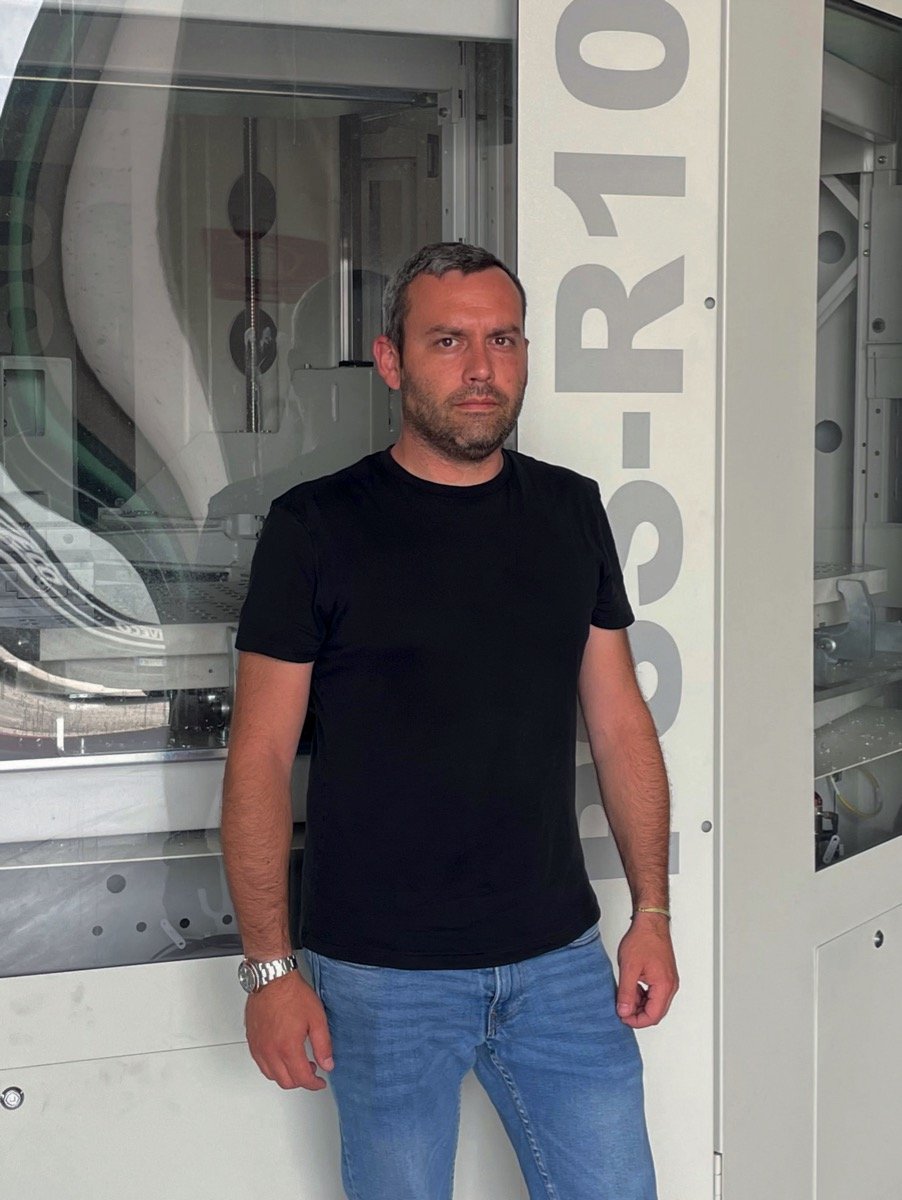
Il direttore commerciale Mattia Gobbato, terza generazione dell’impresa di famiglia