L’azienda di Chiampo (Vicenza) è leader nel mercato con la tecnologia 3D applicata al settore calzature da lavoro. Garantita la maggior efficienza di sicurezza, stabilità e comfort
Cinquant’anni di vita, festeggiati proprio nel 2021, che testimoniano una splendida storia imprenditoriale e familiare, giunta alla terza generazione. A far nascere nel 1971 la GIASCO SAFETY SHOES Srl di Chiampo (Vicenza), furono i coniugi Attilio Scolaro e Mariarosa Gianesini (le cui prime lettere dei cognomi hanno creato l’acronimo di Giasco), il cui figlio, Filippo Scolaro, è l’attuale amministratore delegato.
Da mezzo secolo l’industria veneta, che attualmente dispone di una forza lavoro di 75 dipendenti, produce scarpe antinfortunistiche, rispondenti ai più severi standard mondiali, proponendo prodotti unici per materiali e design. La soddisfazione del cliente e una filosofia “Made in Italy” rappresentano i fattori chiave di una realtà che nel corso degli anni ha sempre registrato una crescita del fatturato e della produzione, capace di imporsi soprattutto a livello internazionale, come conferma la quota export superiore all’85%.
“Esportiamo in una novantina di Paesi di tutto il mondo – precisa il responsabile marketing Ettore Caneva, che abbiamo intervistato in sede, parte della famiglia fondatrice – ma con un’alta percentuale destinata al Centro e Nord Europa, visto che il nostro prodotto è collocato in una fascia medio-alta. Sempre attenti all’etica, al design, alla tecnologia e all’innovazione, operiamo attivamente per il completo soddisfacimento delle attese dei nostri stakeholder. Sono proprio la qualità del prodotto offerto, l’estrema attenzione nei confronti dell’assistenza e l’efficienza e puntualità dei servizi che ci permettono oggi di essere tra i leader nei mercati internazionali”.
La GIASCO SAFETY SHOES è diventata famosa due anni fa per aver brevettato la tecnologia imperniata sulla suola con tri-densità. Di cosa si tratta?
In un mercato caratterizzato da scarpe a due iniezioni, siamo riusciti a realizzare un upgrade, una miglioria a livello tecnico tale per cui i nostri prodotti vantano tre diverse densità, in grado di favorire notevolmente il livello di comfort. Soprattutto nelle scarpe da lavoro la tecnica dell’iniettato, che è poi quella che contraddistingue l’intera nostra produzione, fa la “voce da padrone” perché assicura le migliori prestazioni e la maggior sicurezza, uno speciale grip e con ottimi standard di stabilità.
Quando è avvenuto il debutto sul mercato?
Alla fiera di Düsseldorf nell’autunno 2019 con il lancio sul mercato internazionale del modello 3Run, che rappresenta una linea sportiva, con tre densità parallele e caratterizzato da un fondo progettato prevalentemente per l’attività lavorativa indoor, quindi al coperto. Forti di questa tecnologia, qualche mese dopo, ad inizio 2020, abbiamo allargato l’offerta anche all’outdoor con una scarpa composta da una suola più alta e voluminosa, ma altrettanto comoda, in grado di attutire i colpi e le irregolarità di superficie, tipiche delle aree esterne.
A cavallo tra il 2020 e il 2021 avete lanciato il vostro top di gamma…
È rappresentata dalla linea #3 Hybrid, attualmente il modello di punta: si tratta di una comoda e colorata scarpa antinfortunistica, di grande impatto per sportività e eleganza, che può essere indossata nel tempo libero, volendo anche per giocare una partita di calcio. La #3 Hybrid è una gamma contraddistinta da questa tecnologia brevettata, la suola unica al mondo con densità di 3 PU iniettate, progettato attorno ad una specifica suola concentrata sull’ottimizzazione del suo ammortizzatore.
Quali sono i punti di forza della #3 Hybrid?
È un modello molto bello dal punto di vista estetico, piace in particolare la tomaia. Inoltre la suola con la finestra in cui si vede il colore a contrasto è molto aggressiva, mentre un ulteriore grande valore aggiunto è la morbidezza del fondo, aspetto importante a livello comunicativo in quanto viene percepito facilmente dalla clientela. L’uso totale del poliuretano rappresenta un notevole vantaggio rispetto alle soluzioni con inserti in materiali diversi utilizzate da buona parte dei nostri competitor, soprattutto quando si tratta di scarpe da lavoro che vengono indossate per oltre 8 ore al giorno e in ambienti particolari, dove c’è un’abrasione continua.
Come operate a livello di ricerca e sviluppo nell’ambito della progettazione?
Tutte le linee, prima di essere lanciate sul mercato, hanno un tempo di studio che può variare tra uno e due anni. A partire già dalla realizzazione del disegno alla progettazione per passare alla scelta dei materiali, poi con l’arrivo dei primi stampi pilota procediamo con le iniezioni per vedere che sia tutto a regime. Quindi per un paio di mesi facciamo provare le scarpe, all’interno della nostra fabbrica, per apportare ulteriori eventuali sistemazioni e solo nel momento in cui siamo sicuri che sia tutto a posto avviamo la produzione.
A livello di certificazioni come vi ponete in base alle esigenze del mercato?
Tutti i nostri prodotti sono certificati, aspetto che riteniamo fondamentale in quanto apprezzato dai clienti. In questo ambito il partner della GIASCO è la Ricotest di Pastrengo (Verona), sul lago di Garda, che riteniamo la migliore sul mercato. Dato che il nostro è un prodotto tecnico, oltre alle tradizionali certificazioni già ottenute, cerchiamo sempre di percepire dai nostri clienti le nuove richieste del mercato e insieme a loro andiamo ad approfondire quali altre certificazioni possano essere gradite dall’utilizzatore finale per differenziarci in settori specifici da tutti gli altri. Ascoltiamo con attenzione le indicazioni della nostra clientela nel mondo e spesso riusciamo ad anticipare i tempi.
La vostra azienda come è inserita nel territorio in cui opera?
La Valle del Chiampo, che da sempre rappresenta la culla dell’attività, da diversi decenni è uno dei più importanti centri mondiali per la lavorazione della pelle grazie ad un mix tra conoscenze tecniche artigiane secolari, spirito imprenditoriale e una vision rivolta al futuro. Grazie alla presenza di questo distretto, nel territorio sono presenti eccellenti istituti tecnici specializzati che offrono alle aziende un personale altamente qualificato e competente: entrambi sono aspetti fondamentali per la produzione di calzature antinfortunistiche.
Quali sono i vantaggi principali nell’appartenere al distretto di Arzignano?
Significa approvvigionarsi giornalmente dei migliori materiali in termini di resistenza, eleganza, morbidezza, idrorepellenza e traspirabilità: ad esempio noi acquistiamo il pellame da una conceria situata a pochi chilometri, dove ogni settimana nostri incaricati vanno a verificare la qualità del materiale. Per il resto tutti i nostri produttori sono italiani, mentre per quanto la giunteria e gli stampi lavoriamo con aziende venete.
Infine qual è il vostro impegno a livello di sostenibilità?
Siamo sempre più alla ricerca di prodotti a ridotto impatto ambientale. Sia per i pellami che per i materiali sintetici scegliamo quelli che sono in grado di garantire un maggior rispetto dell’ambiente. Tra i vari progetti allo studio a livello produttivo, stiamo sperimentando varie percentuali di poliuretani riciclati nella suola, a loro volta in grado di poter essere reimmessi in produzione. Consapevoli che l’attenzione all’ambiente rappresenterà anche in futuro un aspetto determinante, l’obiettivo aziendale va al di là del mero risultato economico. Per questo, introducendo nella nostra mission il Comportamento d’Impresa Socialmente Responsabile, ci impegniamo nella massima tutela sociale e in un concreto rispetto dell’ambiente.
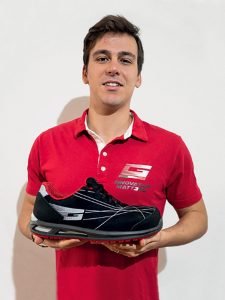
Ettore Caneva Resp. Marketing e R&D