Una visione forte e l’incessante ricerca tecnologica hanno portato l’azienda di Prato a scalare la vetta grazie alle sue lamine antiperforazione ultra-sottili e le tomaie ecologiche ad altissima tenacità.
Ci sono molti modi per definire l’impegno delle aziende che decidono di includere nel proprio business anche la dimensione ambientale, oltre a quella economica. Rudi Priami, General Manager di Manifattura Pri.Ma.Tex, oltre a essere un imprenditore lungimirante è anche un vero innovatore nel settore delle fibre tessili ad alta tecnologia. Collaborare attivamente con i propri clienti per realizzare prodotti di eccellenza, esclusivi ed ecosostenibili, è una delle mission dell’azienda toscana, unica al mondo a partire dalla rocca del filo per arrivare al capo finito.
Come è iniziata questa avventura?
“La mia carriera è cominciata nel 1977 come dipendente di un’azienda molto grande, e altrettanto rinomata, del settore tessile-calzaturiero. Avevo 27 anni. L’azienda aveva due divisioni e produceva prevalentemente tessuti e moquette. Ho occupato la posizione di Responsabile Commerciale Italia per 17 anni, facendone crescere il fatturato in maniera esponenziale con tenacia e passione. Come spesso accade, dopo tanti anni passati all’interno della stessa realtà, sentii il bisogno di dare vita a qualcosa di mio e intrapresi un nuovo percorso come libero professionista. Con successo. Un giorno, il Responsabile di una realtà imprenditoriale che rappresentavo, consapevole della mia grande voglia di fare, mi propose di fondare una azienda insieme a lui: così è nata Manifattura Pri.Ma.Tex.: “Pri” sta per Priami, “Ma” sta per Maiano, “Tex” sta per tessuti. Dopo dieci anni di attività insieme, abbiamo deciso di dividerci per dare spazio anche a mio figlio Christian che stava crescendo all’interno dell’azienda. A quel punto, divenuto unico Direttore Generale, con diretto accesso al mercato, vedevo che l’azienda aveva bisogno di inserirsi in un contesto più tecnico e ho eliminato un po’ alla volta tutti gli articoli civili. Io provengo da una mentalità fortemente legata alla salute perché connessa ai sottopiedi. Questo è uno dei miei argomenti principi. Sono stati proprio i clienti ad invogliarmi ad approfondire e lavorare sulla perforazione tessile”.
Il vostro è un percorso incessante verso la realizzazione di filati altamente tecnologici certificati, anche per tomaie. Corretto?
“Esattamente, in particolare ci riferiamo ai filati in HT, ovvero poliesteri ad alta tenacità. Lavoriamo con nylon e filati riciclati come il New Life, la migliore fibra tessile ecologica di alta qualità, creata con bottiglie di plastica riciclate e prodotta in modo sostenibile. Inoltre tessiamo filamenti mono bava di nylon estremamente resistenti. Per farvi un esempio indicativo della nostra qualità, quando sottoponiamo i nostri prodotti ai test sull’abrasione (facciamo riferimento sempre alla norma EN388) pretendiamo il massimo livello raggiungibile. Su alcuni specifici articoli forniamo addirittura una garanzia di 24.000 cicli che è un livello molto elevato rispetto agli standard richiesti”.
Parlando di standard, da quanto tempo la vostra azienda è certificata GRS?
“Abbiamo ricevuto il “Global Recycle Standard”, che risponde all’esigenza di fornire una dichiarazione ambientale verificata da parte terza che comprovi il contenuto di materiali da riciclo dei nostri prodotti (sia intermedi che finiti) e il rispetto di criteri ambientali e sociali ben definiti, da circa un anno. È stato un percorso lungo e complesso ma ne siamo molto orgogliosi”.
Il GRS impone ovviamente criteri molto alti. Come affrontate le limitazioni imposte?
“Molte aziende, per superare i limiti imposti dal GRS, realizzano tomaie accoppiate con una interfodera in feltro. Questo tipo di lavorazione ne diminuisce traspirabilità e leggerezza, per non parlare della quantità maggiore di calore generato durante l’utilizzo della calzatura. Noi invece realizziamo accoppiatore microforate al poliuretano reattivo, garantendo così la totale traspirabilità. Entrando nel dettaglio, abbiamo ideato un tessuto tridimensionale con due facce identiche. Perché? Sarebbe stato semplice prendere un tridimensionale forato e accoppiarlo alla tomaia ma i problemi che ne sarebbero nati sarebbero stati molti tra cui la cedevolezza alla tensione, quindi minor resilienza. Per noi non è mai stato accettabile un compromesso di questo genere. Con il nostro metodo consistenza e qualità vengono mantenute, insieme a rotondità e morbidezza, completa assenza di grinze nella fase di montaggio della scarpa e una leggerezza impareggiabile. Nel settore della scarpa da lavoro abbiamo raggiunto livelli altissimi grazie ai nostri poliesteri ad alta tenacità”.
Che differenza c’è tra i poliesteri ad alta tenacità e il nylon?
“A livello di resistenza la differenza è abissale. Una volta non esistevano altre alternative al nylon, oggi ci sono. Un esempio è una delle nostre fodere tridimensionali da 280 grammi che ha una resistenza di circa 600.000 cicli. E saremmo potuti andare ancora avanti… Consideri che la norma prevede uno standard garantito di 51.200 cicli”.
Come è stata recepita questa fodera dal mercato?
“In maniera ottima, infatti è stata immediatamente scelta da un marchio di calzature sportive molto rinomato. Le nostre fodere tridimensionali sono uniche. Oltre alla resistenza, possiedono una maggior traspirabilità rispetto a tutte le altre fodere oggi in commercio”.
Per realizzare prodotti di alta qualità è necessario sempre partire dalla ricerca tecnologica…
“Ricerca e sviluppo sono tasselli fondamentali per dare vita a questo genere di prodotti. Siamo dell’opinione che la qualità ripaghi, tardi ma ti ripaga”.
Parliamo del vostro approccio green…
“Per noi è imprescindibile. Abbiamo da poco creato una tomaia 100% naturale realizzata unicamente con il lino che, grazie alla nostra sapienza nella tessitura e nei finissaggi, possiamo testare con la normativa EN388. Credo che la nostra azienda sia l’unica al mondo a poterlo fare con una grana di soli 180 grammi. Su 4 livelli di certificazione relativa alle fibre naturali, con questo prodotto abbiamo raggiunto il 3. Un risultato davvero eccezionale”.
Come riuscite ad ottenere risultati di questa portata?
“Abbiamo macchinari creati appositamente per l’antiperforazione, sia per quanto riguarda i termofissaggi, stampe e applicazioni, oltre a quelle per l’accoppiatura con poliuretano reattivo. Grazie alla presenza di un laboratorio interno, siamo in grado di controllare e certificare tutti i materiali in uscita. La nostra forza è dovuta anche ai brevetti esclusivi, ben quattro, tra cui quello sviluppato insieme allo staff tecnico di Diadora. Noi siamo stati gli unici a realizzare la perforazione a zero con i parametri di traspirabilità della Geox, cioè 2000 milligrammi a centimetro quadro per ora. Infine ne abbiamo preparato un altro, già depositato, che riguarda la perforazione a tre millimetri. Quest’anno abbiamo creato un sottopiede di montaggio a iniezione – a costruzione Strobel – di due millimetri e otto di spessore. Un prodotto completamente flessibile. Infine, per quanto riguarda il GRS abbiamo costruito il tradizionale 4 millimetri, conduttivo e riciclato, o quello con il chiodo da 4,5, morbidissimo. La nostra tecnologia è davvero all’avanguardia!”.
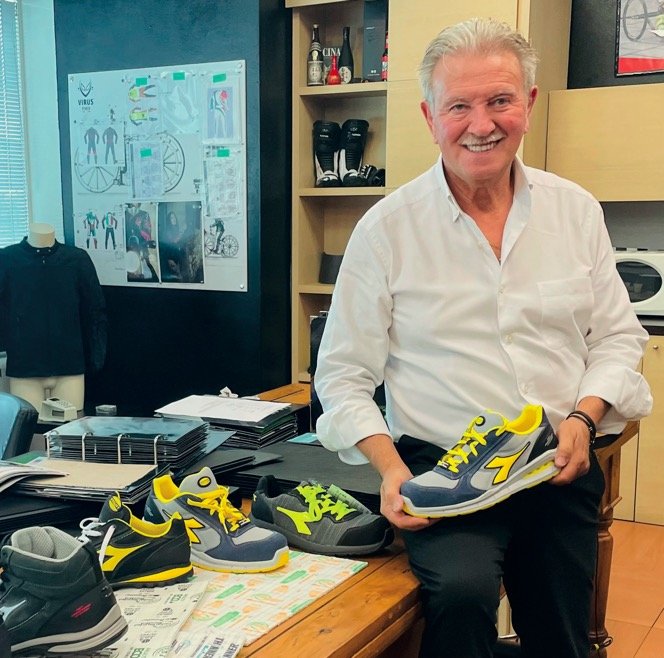
Rudy Priami, General Manager, con una scarpa Diadora con tomaia e sottopiede in tessuti tecnici Pri.ma.tex