ADI-International Chips rivoluziona l’universo della rifinizione dei metalli con ECOS, il sistema che permette la burattatura a secco con preformati abrasivi plastici nato dalla collaborazione con O.M.M. Officine Minuterie Metalliche
Lo sviluppo sostenibile è definito come “uno sviluppo che soddisfi i bisogni del presente senza compromettere la possibilità delle generazioni future di soddisfare i propri”. I processi produttivi e le attività manifatturiere svolgono un ruolo importante nel consumo energetico e idrico del paese. Rispettare una risorsa naturale come l’acqua è un obiettivo possibile, oltreché d’obbligo, grazie anche a nuove tecnologie come quella brevettata da International Chips, che opera anche in settori all’avanguardia come quello aerospaziale. Ecos è una vibrofinitura rivoluzionaria, resa possibile grazie a innovativi cicli di lavorazione completamente a secco. Prodotto in varie misure, forme, densità e porosità, l’innovativo chips è strutturato per garantire la massima efficienza di taglio senza l’ausilio di composti intermediari tra l’abrasivo e la superficie dei pezzi da lavorare. Ne parliamo con Riccardo Bonazzoli, Sales Manager dell’azienda piemontese.
Quando è nata International Chips?
“L’azienda nasce negli anni ’70 in provincia di Verbania, a Domodossola, con l’idea di produrre granuli abrasivi destinati alle lavorazioni tradizionali di abrasione e rifinizione di parti metalliche in genere. In questo caso, ci riferiamo al mondo della moda, quindi all’accessorio. La burattatura serve per trattamenti di asportazione o di lavorazione delle superfici: per renderle più belle o per eliminarne i difetti. Nel corso degli anni, per soddisfare le esigenze di una clientela sempre più ampia, International Chips ha investito molto in ricerca e sviluppo, e in risorse umane, ampliando così la gamma delle sue linee di produzione. Diciamo che, dagli anni ‘70 a oggi, c’è stata una grande evoluzione. Nel 2019, International Chips entra a far parte del Gruppo Surfaces con il quale, grazie alla sua organizzazione e l’estesa rete commerciale, è riuscito a esprimere al meglio il suo potenziale nel mercato mondiale. Pur rimanendo una unità a autonoma, abbiamo avuto l’opportunità di investire massivamente in tecnologia e innovazione, cosa che ci ha permesso di rispondere alle richieste, sempre più pressanti da parte di tutti i produttori di accessori, di migliorare quelli che erano alcuni aspetti legati al prodotto finito. Non bastava più soltanto migliorarlo dal punto di vista estetico, quindi migliorarne la qualità, ma era nata anche l’urgenza di renderlo più ecosostenibile. Parola che nel 2000, anno in cui è nato il progetto Ecos, era un pochino meno conosciuta rispetto a oggi, ma sulla quale noi stavamo già ragionando e investendo energie. Perciò, una delle prime azioni che abbiamo escogitato era quello di eliminare l’acqua dal processo produttivo di questo tipo di lavorazioni”
Nasce così la burrattatura a secco? Dalla richiesta di un cliente?
“Esatto. Si può già intuire che, eliminando l’acqua dal processo, non solo non utilizzo più un bene essenziale che non va sprecato, ma addirittura è possibile ridurre al minimo i residui di lavorazione. Perciò, con questa finitura a secco, abbiamo un doppio vantaggio: riusciamo a ottenere una qualità superficiale migliore, in più lo facciamo con un prodotto ecosostenibile, non produciamo fanghi e limitiamo anche l’annosa questione dello smaltimento. Ci sono voluti ben dieci anni di studio per creare Ecos, ma nel 2008 finalmente lo abbiamo brevettato e abbiamo iniziato a venderlo alle aziende che lavorano per le firme e i marchi dell’alta moda. Nelle Marche, in Toscana, e più in generale nel mondo, abbiamo tantissimi clienti che si sono convertiti a questo nuovo sistema, abbandonando quello tradizionale”.
Siete stati assoluti precursori in tema di sostenibilità e rispetto ambientale: sono già trascorsi 14 anni da quando Ecos è sul mercato…
“Diciamo che siamo stati precursori sì, ma anche molto alternativi perché in grado di assicurare un grosso vantaggio al nostro cliente, a discapito di un sistema obsoleto. Anche in termini di costi. Il percorso è stato davvero molto lungo: non avevamo pensato tanto all’immediato ma piuttosto che una scelta di questo tipo ci avrebbe potuto premiare con il tempo”.
È stato quello che si chiama un investimento a lungo termine…
“Certo, perché anche al nostro interno abbiamo dovuto attuare grandi cambiamenti per arrivare alla produzione di questo tipo di granulo. Abbiamo fatto una scommesso anche se era più facile continuare a produrre quello che tutti avevano già”.
Qual è il futuro di questo sistema? Quali ulteriori sviluppi potranno esserci secondo la sua opinione?
“L’evoluzione che abbiamo in mente, ma che per il momento è di difficile applicazione, è quella del riciclo e recupero totale. Tutti coloro i quali fanno un prodotto che tende a inquinare, oggi, devono poter anche credere che si possa recuperarlo in qualche modo. Ogni qualvolta si utilizza un abrasivo si produce anche uno scarto che, in pratica, diventa polvere. Ad oggi, queste polveri vengono smaltite attraverso specifiche società di recupero perché contenenti metalli, e perciò considerate un rifiuto “pericoloso. Noi stiamo collaborando con alcune di queste realtà per far sì che sia possibile recuperale in un ciclo virtuoso. Non dico che la polvere possa tornare a essere granulo, ma potremmo pensare di utilizzare questo scarto per produrre qualcos’altro, riducendo ulteriormente la possibilità di inquinare. Le soluzioni ci sono già, dobbiamo solo industrializzarle, renderle economicamente vantaggiose. Ci stiamo lavorando”.
La speranza è che diventi buona prassi per tutti. Ma facciamo uno step back: come è nata la collaborazione con O.M.M.?
“Conoscono Giorgio Nerpiti e la sua famiglia da moltissimi anni. Mi chiesero se fosse possibile migliorare il loro reparto di lavorazione e finitura. Al tempo, avevo iniziato da pochissimo la collaborazione con la International Chips. La O.M.M. è stata una delle prime nelle Marche, se non la prima in assoluto, che ha creduto in me. Abbiamo iniziato facendo dei primi test su qualche loro macchina, fino a quando Giorgio ha detto “Ok, la cosa mi piace!”. Così è stato creato il primo impianto. Tutto è nato dalla sua urgenza di risolvere il problema dello smaltimento dei fanghi, a cui, all’epoca, ancora nessuno pensava”.
Un problema che ora è diventato di primaria importanza…
“È un problema enorme, non se ne parla abbastanza. Molte piattaforme ecologiche, su cui prima si appoggiavano tutti per fare smaltimento, ora sono piene. Inoltre, ottenere una concessione per crearne di nuove è quasi impossibile. Per questo motivo noi stiamo collaborando con queste società per cercare di non smaltirlo come rifiuto inerte ma trasformarlo in qualcosa che possa essere riutilizzato”.
Ecos è sicuramente la risposta…
“Noi proponiamo una soluzione economicamente vantaggiosa e sostenibile. Inoltre, diamo l’opportunità, a chiunque voglia risolvere il problema dei fanghi derivanti da questi processi e toccare con mano Ecos, di accedere al nostro laboratorio e fare dei test comparativi. In caso di dubbi o perplessità, invitiamo il cliente in azienda, lo ospitiamo a Domodossola, e gli mostriamo l’intero ciclo di lavorazione, utilizzando anche i loro prodotti ovviamente. Dopodiché possono tornare a casa, fare la galvanica, e tutte le altre lavorazioni del caso, e verificarne il risultato. Se ritiene che il processo corrisponda effettivamente a quanto sosteniamo, come sempre accade, allora procediamo con la conversione”.
Immagino non sia sempre così facile…
“Hanno abbracciato il nostro progetto gli imprenditori più lungimiranti, quelle persone che dicono “No, non dobbiamo andare avanti così, il futuro deve e può essere diverso da questo”. Parliamo di chi fa scelte consapevoli perché vuole essere differente e comprende che rimandare il problema non serve a nulla, anzi peggiora solo le cose. Tutte le soluzioni mirate al miglioramento del benessere del consumatore finale, e di chi ci lavora, come quelle che riducono l’inquinamento, devono essere prese in considerazione. Non possiamo fare più finta che riguarda solo gli altri perché, prima o poi, riguarderà noi”.
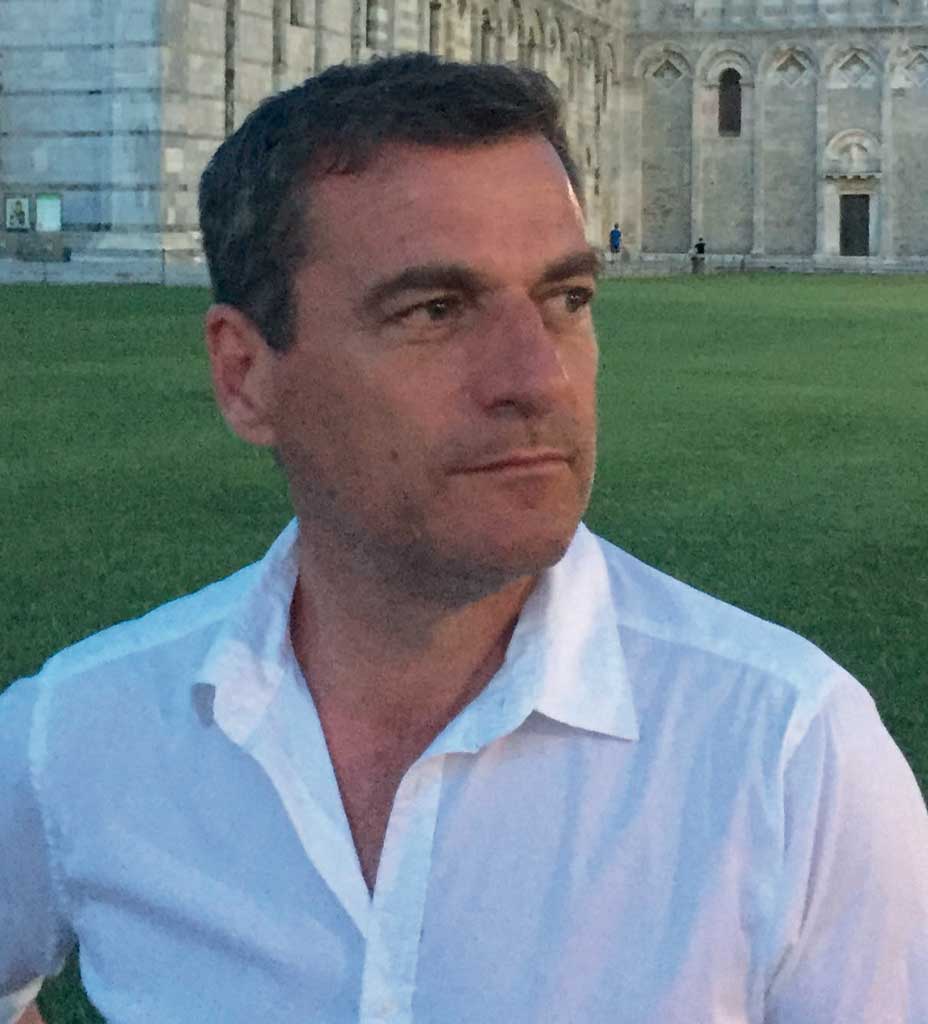
Riccardo Bonazzoli, Sales Manager