AMA Gusberti, a historic company headquartered in Vigevano (Pavia), constantly develops technologies and automations boasting low consumption and reduced environmental impact.
AMA Gusberti is a company based in Vigevano (Pavia) operating since the Second World War in the footwear industry, whose production includes machinery for single- density, dual-density soles, slippers, sandals, fussbetts, technical items, sports shoes and safety shoes. Its products are exported worldwide and companies of the most important footwear districts rely on its machinery. Its history is deeply rooted in the Vigevano footwear district, today still one of the most important nationally.
The company AMA Srl was founded in 1948 and started its business by producing high technology and quality machines. In 1985, following an organizational makeover and the entry of new professional figures, AMA Gusberti srl was founded. Stefano Greco is currently the major shareholder: we interviewed him last September, at the Simac TT show. The renewal implemented by the management has led this brand to quickly be renowned as a world leader in the development of automatic rotary machines for molding polyurethane soles, direct molding on uppers and other technical items. In recent years, the company focused reducing on energy consumption though new technologies and on automation systems able to guaranteeing savings in molding materials, release agents and, where possible, water washing.
“Since the mid-eighties – states Stefano Greco – AMA Gusberti has established itself in the world of casting machines for the production of soles and is still a leader in this sector. Currently in the market we are among those that produce the largest number of casting machines for the production of soles in the fashion sector. I was just over 20 years old when I joined the company in 1999 as a mechanical designer, which is the profession linked to studies, and gradually I began to cover several roles. After having developed many prototypes and innovative projects, in 2015 my role has changed, after the shares’ purchase. As a matter of fact, even before this date I felt it was “my company”, so it was a kind of natural transition. In recent years we have developed many patents in different sectors, both for casting machines and for injection machines.”
What is your flagship?
“Certainly, is the production of casting machines. Not only because we believe they are suitable for making bottoms, but because they can produce shoes much faster than an injection machine. The production rate of a machine that makes shoes by casting is double compared to an injection machine, and it also boasts considerably lower costs. As a matter of fact, at least potentially, there would be the possibility of replacing a casting machine instead of two injection machines, aiming at reducing the energy costs considerably. At the Milan fair we displayed one of the casting machines that we developed: it can produce 200 pairs per hour, compared to 100 pairs of an injection machine.”
A pivotal role of molding costs is played by manpower.
“It is the real issue, manageable only thanks to a greater process automation. In Ama Gusberti we have focused a lot on this subject, for some time we have established an important collaboration with Robot System: they are complementary to us and vice versa, all projects are developed together. They are acknowledged in the footwear industry as great experts, they represent excellence. We unceasingly dialogue with them, we develop projects together, there is a tight cooperation and we often attend international fairs together.”
According to the current economic situation, what are the main requests coming from the market?
“We establish a very close relationship with our customers, we always try to satisfy them and meet every need, both for those who use casting plants, such as some sectors of fashion, and for those who prefer injection systems, mostly chosen by military or safety footwear producers.
Our designers are constantly developing new projects, for example we have a patent on a completely brushless mold holder to be able to automatically control the closure of the bottom, which has always been the main problem in the world of injection. As a matter of fact, the manual adjustment of the bottom of the two stages doesn’t exist anymore, as the system is managed by a very high-performance electric driver, which allows to manage the closing force, the speed and store and transfer the molding data from a machine to the other. We foresee a strong development of these systems but on the other hand we cannot think of revolutionizing the sector in a few years: that’s why several of our customers use both types of machines, it will be up to them to make the choices for the future.”
What about your environmental commitment?
“First of all, building much more productive machines is already a step towards sustainability, considering that we can really save energy. We have also designed systems to use recycled polyurethane, uo to 50%: it is a mixture of polyurethane combined with a part of recycled material; we have already produced several machines like these, they are particularly appreciated for making insoles. We use low energy consumption motors and components, we rely on particular systems for dosing the release agent to avoid overspray, and we endorse sustainable packaging. When possible, we tend to do ecological washes, even with water. The world of fashion firmly demands a responsible attitude from suppliers and we are proud to do our part.”
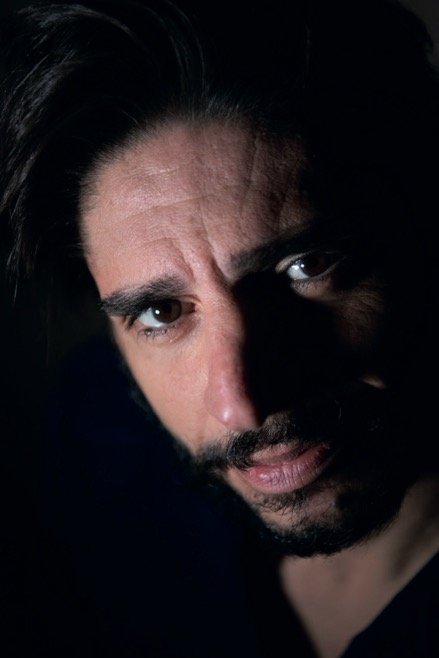
Stefano Greco
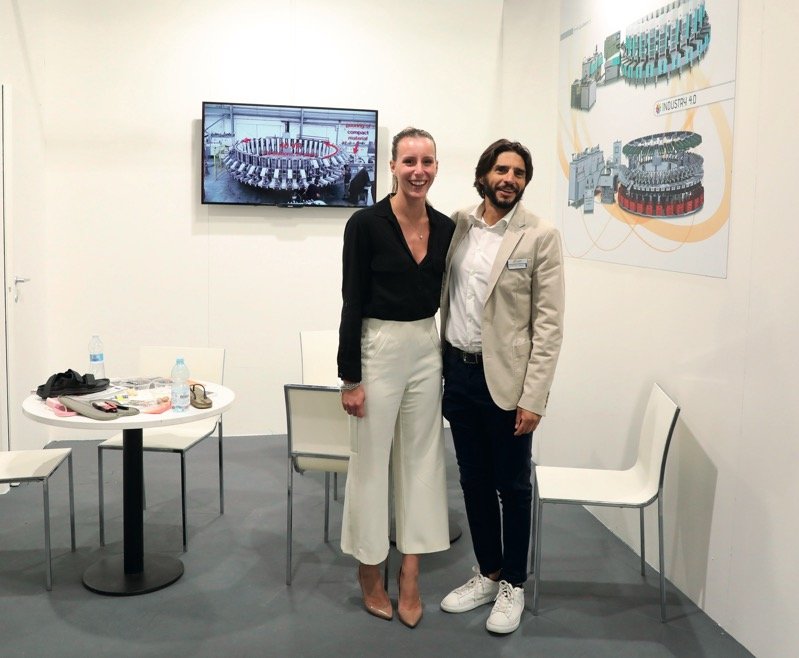
Stefano Greco and Lavinia Marzorati at AMA Gusberti’s stand at the latest edition of Simac fair