ADI-International Chips revolutionizes the universe of metal finishing with ECOS, the system that enables dry tumbling with pre-formed abrasive plastics created in collaboration with O.M.M. Officine Minuterie Metalliche
Sustainable development is defined as “development that meets the needs of the present without compromising the ability of future generations to meet their own needs.” Production processes and manufacturing activities play an important role in the country’s energy and water consumption. Respecting a natural resource such as water is a goal that is possible but also mandatory, thanks to new technologies such as the one patented by International Chips, which also operates in cutting-edge sectors such as aerospace. Ecos is a revolutionary vibrofinish, made possible through innovative all-dry processing cycles. Produced in various sizes, shapes, densities and porosity, the innovative chips are structured to ensure maximum cutting efficiency without the use of intermediary compounds between the abrasive and the surface of the workpieces. We speak about the subject with Riccardo Bonazzoli, sales manager of the Piedmont company.
When was International Chips established?
“The company was founded in the 1970s in the province of Verbania, in Domodossola, with the idea of producing abrasive granules intended for traditional abrasion and finishing processes on metal parts in general. In this case, we are referring to the fashion world, and so to accessories. Tumbling is used for removal or machining treatments of surfaces: to make them more beautiful or to remove defects. Over the years, in order to meet the needs of a growing customer base, International Chips has invested heavily in research and development, and in human resources, therefore expanding the range of its production lines. Let’s say that, from the 1970s to today, there has been a great evolution. In 2019, International Chips became part of the Surfaces Group with which, thanks to its organization and extensive sales network, it has been able to express its full potential in the world market. While remaining a stand- alone unit, we had the opportunity to invest massively in technology and innovation, which allowed us to respond to the increasingly pressing demands from all accessory manufacturers to improve some aspects related to the finished product. It was no longer enough just to improve it aesthetically, but improving its quality and the urgency to make it more environmentally sustainable had also arisen. A word that in 2000, the year the Ecos project was born, was a little bit less known than it is today, but on which we were already thinking and investing energy. Therefore, one of the first actions we came up with was to eliminate water from the production process of this type of processing.”
Is this how dry tumbling was born? From a request of a client?
“That’s right. You can already guess that by eliminating water from the process, we are no longer using an essential commodity that should not be wasted, but we can even minimize processing residues. Therefore, with this dry finish, we have a double advantage: we can achieve a better surface quality, plus we do it with an environmentally sustainable product, we do not produce sludge, and we also limit the age-old issue of waste disposal. It took a good ten years of study to create Ecos, but in 2008 we finally patented it and started selling it to companies working for high-fashion names and brands. In Marche, Tuscany, and more generally around the world, we have many customers who have converted to this new system, abandoning the traditional one.”
You have been absolute forerunners when it comes to sustainability and environmental compliance: it has already been 14 years since Ecos has been on the market…
“Let’s say we were forerunners yes, but also very alternative because we were able to ensure a big advantage for our customer, at the expense of an obsolete system. Also in terms of cost. The path was really very long: we had not thought so much about the immediate but rather that such a choice could reward us with time.”
It was what you call a long-term investment….
“Of course, because even internally we had to implement big changes to get to the production of this type of granule. We took a gamble even though it was easier to keep producing what everyone already had.”
What is the future of this system? What further developments can there be in your opinion?
“The development we have in mind, but which is difficult to implement for the moment, is that of complete recycling and reuse. Everyone who makes a product today that tends to pollute must also be able to believe that it can be reclaimed in some way. Whenever an abrasive is used, waste is also produced, which, in practice, becomes dust. To date, these powders are disposed of through specific collecting companies because they contain metals, and therefore considered a “hazardous” waste. We are working with some of these companies to make it possible to reuse them in a virtuous cycle. I am not saying that the dust can go back to being granules, but we could think about using this waste to produce something else, further reducing the possibility of pollution. The solutions are already there, we just need to industrialize them, make them cost-effective. We are working on that.”
The hope is that it will become good practice for everyone. But let’s step back: how did the collaboration with O.M.M. come about?
“We have known Giorgio Nerpiti and his family for many, many years. They asked me if it would be possible to improve their manufacturing and finishing department. At the time, I had very recently started the collaboration with International Chips. O.M.M. was one of the first in the Marche region, if not the first, that believed in me. We started by
doing some initial tests on some of their machines, until Giorgio said, “Okay, I like this!” So the first system was created. It all stemmed from his urgency to solve the problem of sludge disposal, which, at the time, no one was thinking about yet.”
A problem that has now become of primary importance….
“It’s a huge problem; it’s not talked about enough. Many ecological platforms, which everyone used to rely on for disposal, are now full. Also, getting a concession to create new ones is almost impossible. That’s why we are working with these companies to try not to dispose of it as inert waste but turn it into something that can be reused.”
Ecos is definitely the answer…
“We propose a cost-effective and sustainable solution. We also give the opportunity, to access our laboratory and do comparative tests, to anyone who wants to solve the problem of sludge from these processes and experience Ecos firsthand. If there is any doubt or uncertainty, we invite the customer to the company, host them in Domodossola, and show them the entire processing cycle, also using their products of course. After that they can go back home, do the electroplating, and all the other processing involved, and verify the result. If they feel that the process effectively corresponds to what we claim, which is always the case, then we proceed with the conversion.”
I imagine it is not always so easy…
“The most forward-looking entrepreneurs have embraced our project, those people who say, ‘No, we should not go on like this, the future must and can be different from this.’ We are talking about those who make conscious choices because they want to be different and understand that putting off the problem does no good, in fact it only makes things worse. All solutions aimed at improving the welfare of the end consumer, and those who work there, such as those that reduce pollution, must be considered. We can no longer pretend that it only affects others because, sooner or later, it will affect us.”
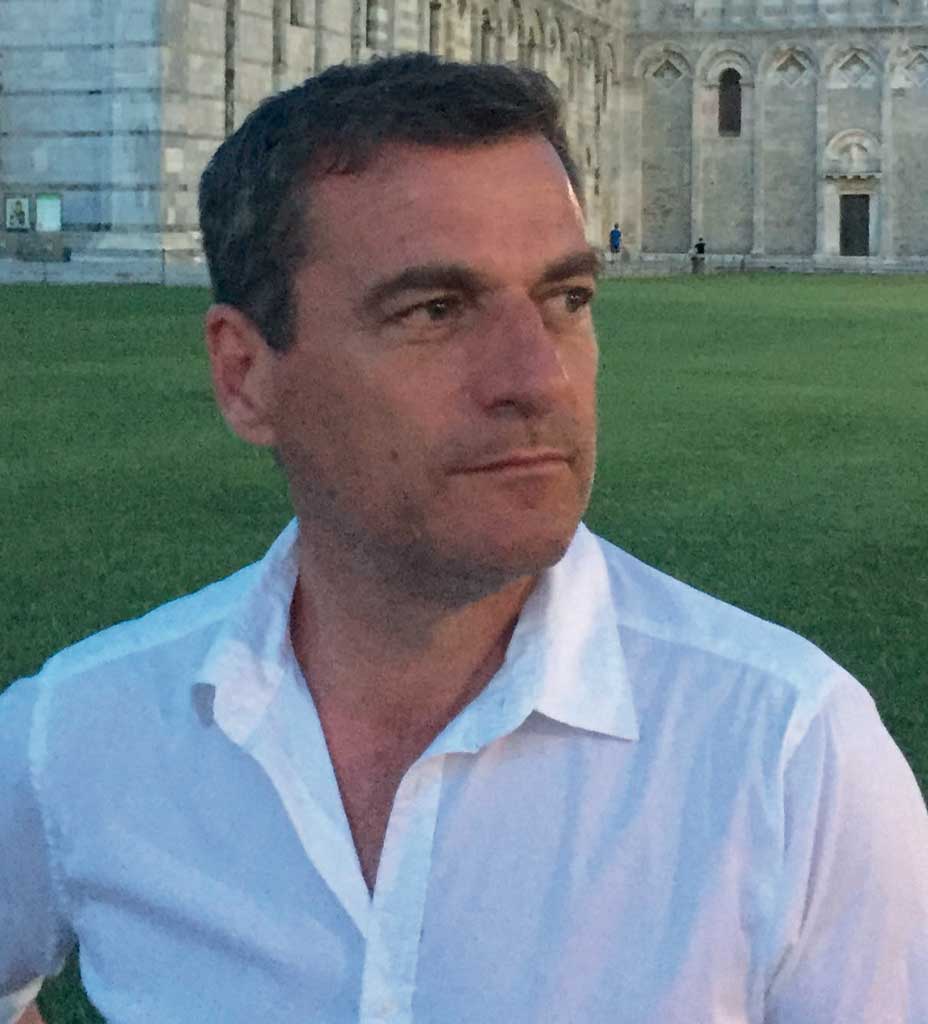
Riccardo Bonazzoli, Sales Manager