The onset of the 21st century has marked great developments in technology and science. However, these developments have come with a price, one of which is aggravated global warming, leading to sudden climatic changes. In order to survive and be productive in such conditions, there is a need for appropriate apparel and shoes for people specifically working in outdoor environments. Waterproof products are engineered with the aim of protecting the wearer from weather conditions like wind, snow and rain as well as preventing excessive loss of body heat.
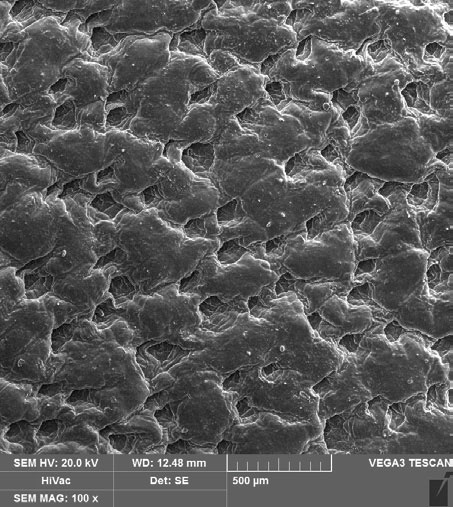
Figure 2. Cross-section images of leather (300x)
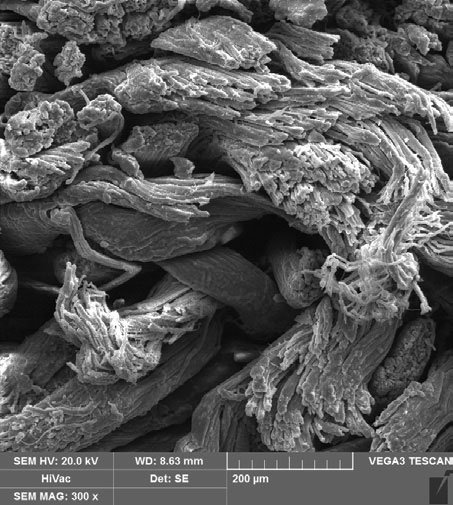
Figure 3. Surface images of leather (100x)
Under normal conditions, cross-section of the leather has a natural fiber weave structure (Figure 2), so it absorbs water by absorbing certain amount of water. The surface of the leather consists of pores in a porous structure (Figure 3). The penetration of water either outside or from inside of leather is largely depended on the wettability of the leather fibres. For this reason, leather products used especially in winter get wet when exposed to humid environment. The water absorption feature should be limited in order for the leather to maintain its strength and its shape. Consequently, the water resistance properties of leathers under dynamic and static conditions are important for the protection of usage hygiene and physiology.
This wettability of fibres varies according to the type of tannage and also the type of leather is concerned. A vegetable tanned leather soaks up water more rapidly than a chrome tanned leather because the fibres are relatively easy to wet whereas the tanned fibres resist water penetration. Upper leathers are made more water resistant because water mostly enters at the leather edge or through the upper stitching. During its production, leather is hydrophobed in various ways to meet customer demands. To achieve the required specifications and properties like high water vapour transmission, high water resistance and better durability, it is necessary to use an optimized combination of hydrophobic and hydrophilic components in the applications. Lubricants used in leather production are one of the main factors in obtaining hydrophobic leather and reducing the water absorption of leather. Since the production of hydrophobic leather is also done in an aqueous environment, the chemicals used must somehow be dissolved in water, that is, they must contain hydrophilic groups that are compatible with water.
Determination of water resistance properties in dynamic conditions is important for determining the water absorption properties of leather goods, especially for an out-door walking shoes during usage because the mechanical action during measurement simulates the mechanical action during walking in water. Dynamic and static water absorption of leathers were given in Table.
The leather obtained by using UNIOIL WPX technology shows high waterproofness after 6 h of testing (water uptake is 12,97 %), while the water absorption rates of the control group samples were given as 142.7% under dynamic conditions. Usually, it is required that military leathers would be water resistant by six hours at least. This means that, after undergoing dynamic testing that simulates actual wear conditions, water absorption should not exceed 25% – 30%. Similar results were also found in the static water absorption test results. It can be noted that the application of water repellent silicone derivative and oil component with aqueous acrylic polymer
solution show very high-water resistance properties to the leather. Evaluation of the UNIOIL WPX showed that the waterproofness for leathers mainly is achieved by filling the gaps in the fibre network with water-in-oil
emulsion and additionally is created using hydrophobic material net around the fibres.
One of the other essential qualities required for an upper of a shoe is to pass air and water vapour because it provides a great comfort to the wearer. Ability to perspirate and subsequent removal of perspiration by evaporation or by absorption is essential for body comfort. In the fabrication of waterproof leather, whereas the penetration of liquid water ought to be prevented, water vapour have to pass the leather as freely as conceivable, or at fewest be absorbed, for ensuring excellent acclimatization inside of the footwear.
Investigated leathers breathability is presented in Table. As can be seen, water vapour permeability (WVP) of leather is slightly affected by application of waterproof properties.
What is the difference with the water-repellent product range that companies already offered?
United Chemicals presented a broad range of innovative solutions for leather processing and footwear customers. The solutions of our company focus on better protection of the environment, efficient use of resources and improved consumer protection. Thanks to UNIOIL WPX, we’ve developed a high-performance waterproofing leather process that has low environmental impact. This new system represents a major milestone because it moves away from the paraffin-based treatment process and switches to a more polymeric approach, which offers many technological and environmental advantages.
With this mission, United Chemicals introduced new recipes for waterproof leather.
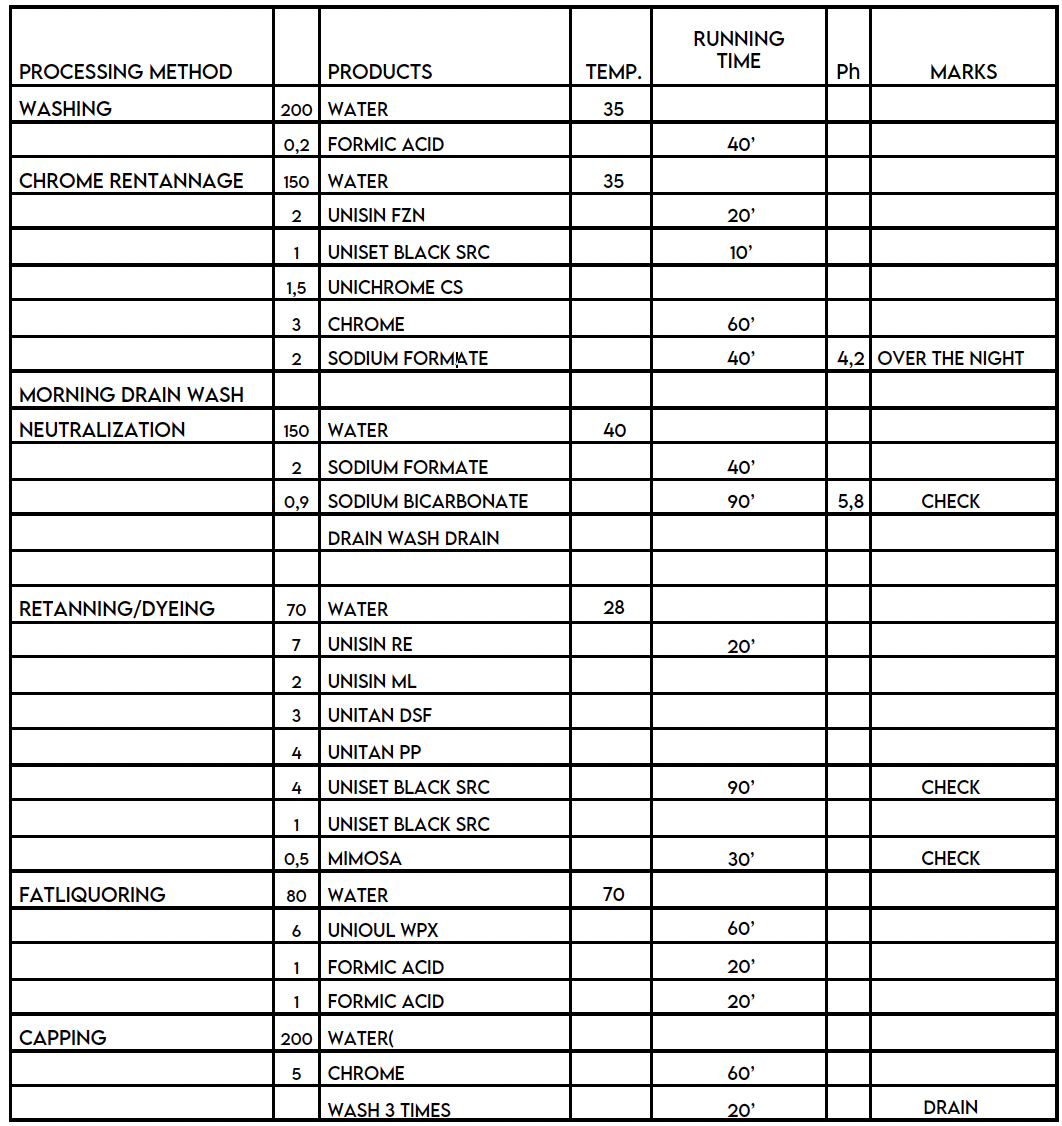
The performance of UNIOIL WPX as a waterproofing agent shows the following properties:
– Leathers that are waterproofed using this system have a higher yield, last longer and show better technical and physical resistance. Additionally, they possess better vapour permeability when compared paraffin treated leather
– The consumption of water in overall post tanning processes are low
– Process control is easy for achieving the optimum expected results
– The waterproofing agents used in this new technology can be incorporated into different stages of the tanning process, while water-proof finishing products are effective at a specific point during the process
– Waterproof crust obtained can be finished, easily with application of different finishing techniques
– Does not require a change of machinery and technology by tanneries
– Does not contain any paraffin derivatives
– Same breathability properties as untreated leathers
At the same time, the chemicals used must have hydrophobic groups because we want to reduce the water absorption rate of the leather. The lubrication emulsions used are bounded to the leather with their reactive groups, allowing a certain amount of water to be absorbed into the leather. The oil-in-water emulsion is penetrated into the leather and takes the form of water-in-oil emulsion. The oils cover the leather fibers with a hydrophobic layer with very low surface tension. Water vapor can enter between the fibers; however, hydrophilic water droplets have high surface tension and do not spread to the hydrophobic fiber surface and only wet the inner surface. For these purposes different types of oils, polymeric products, natural and petroleum derivative fatliquors are being used in fatliquoring process. On the other hand, lubricating polymers are a good alternative to provide water-repellent properties to leather as well as their filling effect with softening and retanning features.
A New Magic Touch to the Waterproofing of Leather: UNIOIL WPX
United Chemicals R&D laboratories presents an innovative technology based on emulsified and esterified polyacrylic polymers with suitable silicones that could be the new benchmark for water-proofness treatments.
UNIOIL WPX is a new generation hydrophobic lubricant for
efficient waterproofing for leathers. It is a white paste with pH-Value 6.5 ± 0.5 and has anionic charge and contains 40 ± 2% active substance. It is a special fatliquor and advised for many types of leathers where hydrophobic properties are required. UNIOIL WPX is perfectly pourable liquids that easily emulsify in water.
UNIOIL WPX has also high softening properties and leather gains fullness and a nice touch. Besides, waterproofing it is recommended for the production of washable leathers. UNIOIL WPX is applied during the main fatliquoring process together with selected fatliquors for the special shoes, garment, upholstery and leather goods types of leathers. The ideal amounts depend on the thickness and end usage of the leathers. But, for heavy boots – such as hiking/military shoes 6.0 – 10% on shaved weight and for light leathers, such as, for garment-nappa, 4.0 – 6.0%, for upholstery 6.0 – 10.0% give satisfactory results.
How Does UNIOIL WPX Work?
The new system is based on a new generation of polymeric agents that are free of solvents and benzene. These materials meet all the requirements set by the ZDHC standard, which makes them safer than current alternatives. UNIOIL WPX are bounded to the fiber of the leather with a 99% exhaustion rate, which is an improvement over oil- or paraffin-based treatments. Ester groups and silicon–oxygen groups promote chemical reactions and increases the binding of the fatliquor emulsion to collagen network. This process also requires less water and lower temperatures, both of which have major benefits for the carbon footprint and water footprint at the tannery that employs it.
In order to demonstrate the water-repellent properties of leathers treated with UNIOIL WPX, the dynamic water resistance of the leathers was examined using the Bally Penetrometer test device according to TS 8541 EN ISO 5403 standards. Determination of the static water absorption of leathers was carried out in the kubelka apparatus according to the TS 4123 EN ISO 2417 test method. With this study, the amount of water absorbed during immersion of leathers was determined at the end of 30 minutes, 1 hour and 24 hours. Moreover, the water vapor permeability analysis was carried out as specified in TS EN ISO 14268. The method was performed in a conditioning room with 20 ± 2 °C temperature and 65 ± 2% relative humidity. The results were calculated in milligrams of water vapor per square centimeter (mg/cm2.h) according to the formula WVP= m/πr2. h.
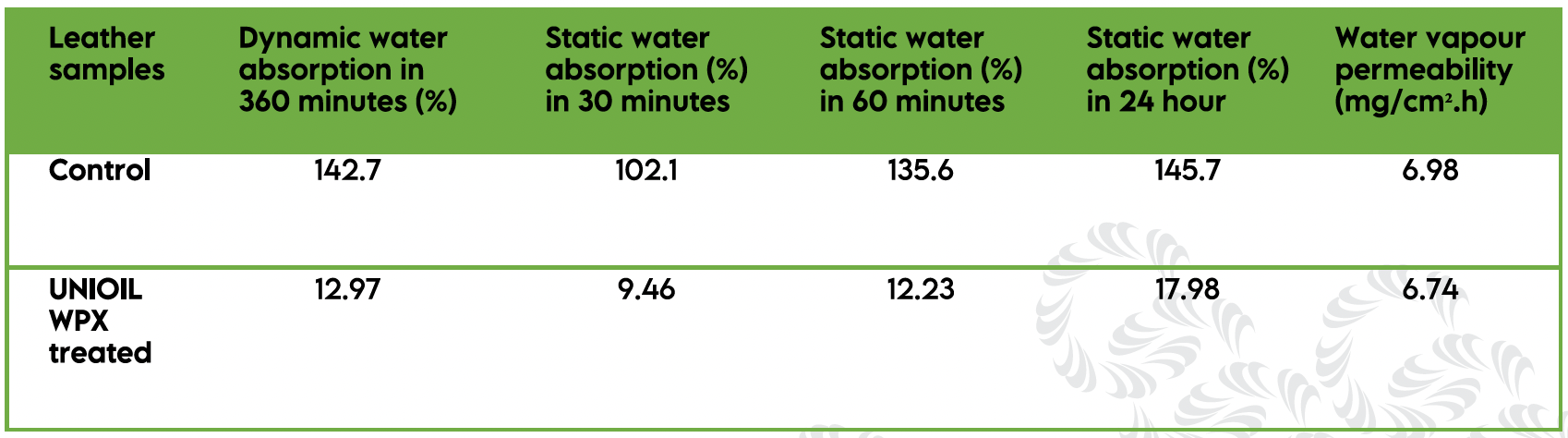