Ambrosetti, leader in the production and marketing of small metal parts used for fashion, interior design and other sector, boasts decades of experience, as it’s on the market since 1979. The company, based in Varese, a city whose leather goods tradition is deep-rooted, stands out among the top players in the sector also thanks to the ability to enhance purely technical items, turning them into real fashion accessories, a perfect combination between functionality, outstanding performance and accuracy. According to the customer’s requests and the specific destination sector, surface treatments are carried out, such as galvanic finishes, glitter effect dyes, enamelling, laser and diamond processing. These processes are mostly carried out in a modern, specialized technological plant, where an infinite variety of graphic and decorative motifs are created. Almost all of the Ambrosetti brand production is marketed internationally, in particular in the European Union and in the Middle East; its items are renowned for the high levels of functionality and aesthetic research as well as for their full compliance with the highest quality standards and with all regulations related to environment protection and safety. To get to know the Ambrosetti business even more closely, we met Davide Ambrosetti, CEO of the Lombard company.
The past two years have been difficult for everyone, and despite the last year’s first signs of recovery, there are still many challenges. How are things going right now?
“In my opinion, it seems that a positive trend has already begun at the end of last year. We do not yet have the exact figures but we feel a significant recovery in the sector. Our company, since September 2021, had already recovered well compared to 2020 and now we reached the growth level of 2019. Fortunately, we have overcome the economic stagnation generated by the pandemic and have returned to the previous turnover.”
In recent years, many companies have optimized in-house process; did Ambrosetti also undertake such path?
“Moving to a new headquarters has been a booster to face a change, an opportunity to look forward and improve. As a matter of fact, we have had the chance to design and develop many new and exciting ideas. I must say that, in the old headquarters, we were in a sort of comfort zone, while in the new one, we’ve been kind of forced to rethink the functioning of workflows, also having the opportunity to update every aspect of the company. In this period, we are investing in several production management resources, not disregarding any aspect of cost and time optimization such as, for example, the documents digitization. These changes and investments are not easy to carry out because they require a change of the single person and a different mental approach towards the company work as a whole.”
I guess these changes require some time to adapt.
“Yes, but the timing is influenced, above all, by the attitude and preparation of each element of the company. At Ambrosetti’s there is no competition and everyone has been very collaborative in tackling a process started with environmental certifications, the certification of the organizational system according to law 231, the codes of ethics and everything related to our production model. Certifications are becoming an essential guarantee for customers.”
What are customers asking for today?
“Currently, to be in line with the needs of the market, the fashion sector is increasingly caring about environmental aspects: footprint reduction, social rights and so on. Soon, the whole system will move in this direction and access to credit will be facilitated for all those companies that will have high- profile environmental parameters compared to those that do not have them. For banks, in addition to financial solidity, these aspects, which have become considerably important, also count a lot. According to his, a census of ESG aspects (Environmental, Social and Governance) is being launched, proving that a process is already underway.”
Was this process boosted by the 2030 Agenda for Sustainable Development and the Paris Agreement?
“We have already carried out many changes according to waste and consumption reducing, such as the drop in plastic and paper use. Our company has been in line with these rules for a long time, now it is only a matter of formalizing it and be certified by a body in charge. Last year we embarked on a formal process focusing on business management. So, for now, our action is directed towards an adaptation of the organizational system, in line with the code of ethics and with law 231. The latter is an Italian law against company crimes and represents the first step to update the business organization system.”
Is all of this an expensive procedure?
“Yes, of course. The first is in terms of bureaucratic time. Then there are the actual costs of the registrations. If you get a certification, rightly so, you must also keep it up to date. In recent years, all of our customers have increasingly raised the bar from this point of view. So, there is a lot of work behind to show our environmental commitment, that we do not exploit employees, that we have an efficient and active workplace safety system, etc. However, you must always prove all of this by providing documentation to the customer. A laborious system at the moment that will be easier when the certifications are effective. By doing so, all systems are managed well and this also allows us to relieve the pressure deriving from customer requests.
We work for many major fashion brands and, as their direct suppliers, we must make sure that our products comply with environmental, social and safety standards.”
What are the trendiest metals and finishes?
“Many companies are replacing the use of brass with that of stainless steel. Such choice is due to the fact that stainless steel doesn’t need any a galvanic finish.”
Are you ready for it?
“We are currently working on it, but it is not really easy: unlike brass, made up of a part of copper and a part of a very ductile material, stainless steel is a very difficult metal to work with as it’s very hard and abrasive and wears out the equipment used. Brass, on the contrary, has better deformability features. However, it is a whole world to discover, an interesting business in an industry that is constantly evolving.”

Davide Ambrosetti
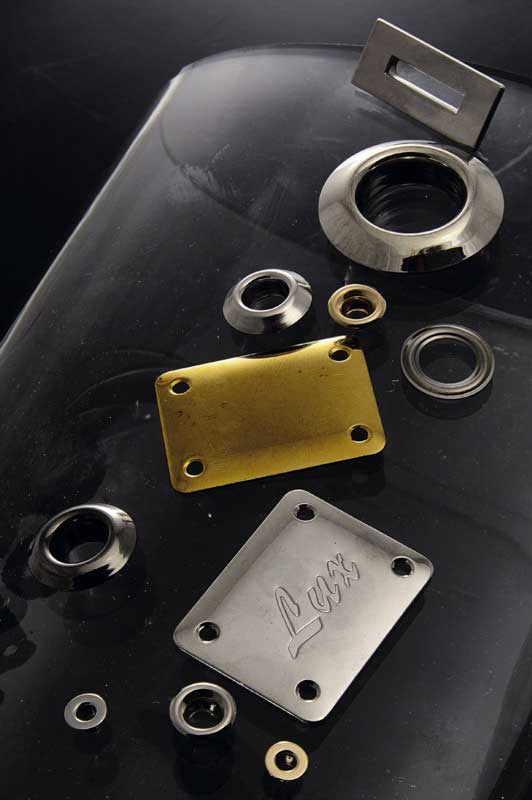