DESMA, leader in the technologies for the footwear industry based in Achim, Germany, stood out once again at the latest edition of the Simac Tanning Tech fair thanks to its ground-breaking solutions. The company, which has recently celebrated its 75th birthday, launched a series of outstanding proposals, as always innovative, functional and environmentally friendly.
It’s been two long years, but it was worth waiting: “Due to the pandemic – Managing Director Klaus Freese explained us at Desma’s stand – we had, like everyone else, a lot of spare time that we used to improve some projects. Today we proudly show them here at the fair and the feedbacks from the customers are more than positive.”
For 75 years, Desma has been designing and developing cutting- edge solutions for the footwear sector, pursuing an uncompromising quality policy in design, production, distribution, assistance and maintenance. Unceasing R&D activities are at the origin of the company’s progressive market penetration and international technological leadership, assisted by constant product optimization in terms of reliability and efficiency, but also by industrial safety and environmental compatibility.
These months have allowed you to complete or improve some important projects.
Desma has always been a byword for innovation, technology, modernity; we are an international reference point for the market and, in terms of research and development, we have never stopped. Of course, the slowdown in the sector has allowed us to devote much more time to our usual studies, leading us to develop several innovative solutions. Among these, the Multi-Section-Injection (MSI – Multi-Section Injection) undoubtedly stands out. This technology is meant for the production of customized PU midsoles: it is possible to have different features in a single PU midsole and also have different features in different sections of a single sole. This system is already used, but we have further improved it: together with the possibility of injecting different colors and materials, it allows designers to give free rein to style, colors and shapes.
Therefore, is this system useful to different application sectors?
Absolutely. We receive a lot of requests especially from sports shoe manufacturers, considering the technical characteristics that can be obtained: according to the type, the compound can be integrally softer or harder, or it can be softer, for example, only on the toe, leaving greater hardness on the heel. The strength of this system is its versatility and the infinite types of customization that we can offer, not only in terms of aesthetic, but above all in terms of functionality: our goal is to create a high-performance sole for a perfect shoe.
Have you also presented any news in the automation sector?
Of course, automation and software are two of our most active departments, especially following the advent of industry 4.0, which is essential today: automation minimizes the consumption of resources and materials, shortens the transport distances and constant quality makes the products secure and durable.
We have developed cutting-edge systems for the remote control of machinery and production data, which are easily stored on a virtual cloud. This technology speeds up times, increases production and is able to create a data history, very useful to make market analysis and corporate income evaluations. In addition, we have already been offering customers the opportunity for rapid diagnostics through DESMA’s modern online service, which, by connecting remotely, quickly identifies problems and solves them on the spot, thus reducing downtime.
You mentioned the resources consumption reduction. What can you tell us about environmental sustainability? What actions did Desma take in this regard?
This is the topic of the moment. To be honest, for several years now we have been talking about methods for sustainable production, and Desma has always been a precursor in this field. Far before this issue became so popular, our policy was already in line with the circular economy’s pillars: in the production of soles, the waste material was re-granulated and mixed with the virgin product, in order to obtain a good percentage of recycled material which, in turn, could have been reused again. This practice, however, was initially required only by the big brands in the sector, since smaller shoe factories could not afford to bear the costs. Even the producers themselves did not particularly appreciate it, because they were afraid that the sole made with recycled materials would not perform well as a “new” one. Clearly, over time the recycling techniques have been improved, the demand has started to grow as well as the supply: today it is our priority to create energy-saving technologies, ensuring low environmental impact and offering products able to improve quality and environmental balance.
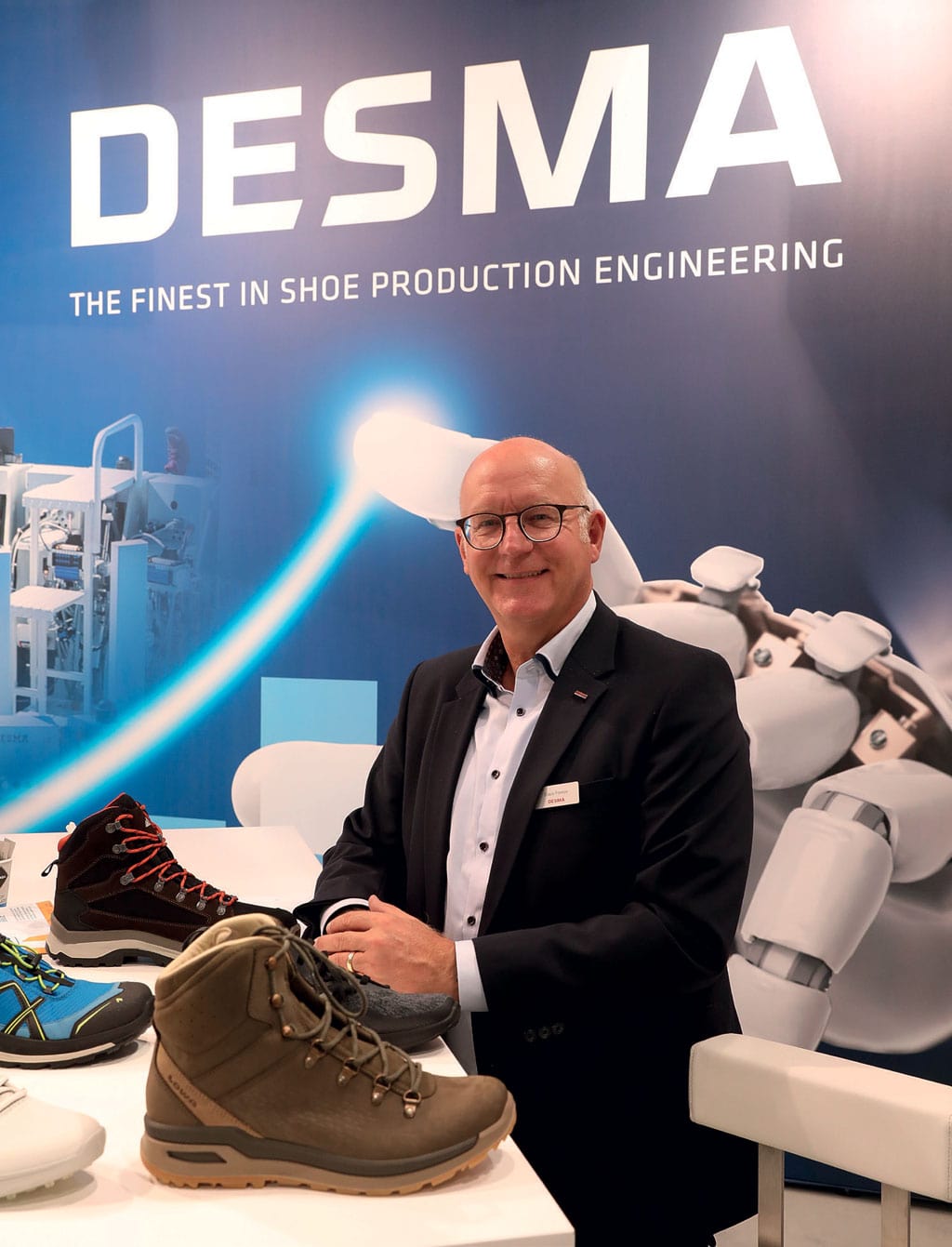
Desma Managing Director Klaus Freese at Simac Tanning Tech company’s stand