Headquartered in Chiampo (Vicenza province), GIASCO is a market leader with the 3D technology applied to the safety footwear sector. It manages to guarantee a higher efficiency in terms of safety, comfort and balance
Fifty years in the business, celebrated in 2021, bearing witness to an amazing family and entrepreneurial history, now in its third generation. GIASCO SAFETY SHOES Srl was founded in 1971 in Chiampo (Vicenza province) by the spouses Attilio Scolaro and Mariarosa Gianesini (the first letters of their surnames formed the acronym Giasco); their son, Filippo Scolaro, is the current managing director.
For half a century, the Veneto-based enterprise, currently featuring a workforce of 75 employees, has been manufacturing safety shoes, compliant with the world’s strictest standards, thus providing unique solutions design- and material-wise. Customer satisfaction and a “Made in Italy” philosophy are core values pursed by a firm that, over the years, has always been able to register a growth in both the turnover and productivity, as well as able to gain a strong foothold internationally, as confirmed by its exports share, over 85%.
“We export to approximately ninety countries worldwide,” explained Ettore Caneva, marketing manager, who we interviewed at the corporate headquarters, part of the founding family, “a high percentage represented by Central and Northern Europe, given that our product belongs to a mid/high-end market segment. With a keen eye for ethics, design, technology and innovation, we are thoroughly bent on fully meeting the expectations of our stakeholders. The quality of the products we provide, the utmost attention in terms of assistance activities, the efficient, prompt services: these are the distinctive traits that have helped us become one of the leaders in foreign markets.”
GIASCO SAFETY SHOES rose to fame two years ago after filing a patent for the technology based on the triple density sole. Can you tell us more?
In a market characterized by double-injection shoes, we have managed to implement an upgrade, a technical improvement, so much so that some of our products feature three different density degrees, able to markedly increase the level of comfort. As for the safety footwear field, the injection technique, that is, the one that marks our whole production, is definitely the most popular, because in ensures top-notch performances and the utmost safety, a special grip, and excellent balance standards.
When did the market debut take place?
At the exhibition held in Düsseldorf in fall 2019, with the launch on the international market of the model 3Run, namely, a sporty line with three parallel densities and featuring a sole mainly designed for indoor work activities. Relying on this technology, a few months later, early 2020, we widened our scope to the outdoor as well, by providing a shoe boasting a higher, more voluminous, yet equally comfortable sole, conceived to absorb the shocks and the surface unevenness, the latter typical of outdoor areas.
Between 2020 and 2021, you launched your top-of-the- range solution…
It is the #3 Hybrid line, namely, our current flagship: a colourful, comfortable safety shoe, standing out for its elegance and sporty design, that can be worn in one’s spare time, even to play a football game. #3 Hybrid is a range of models provided with this patented technology, the only sole in the world featuring a triple density of injected PU, purposefully devised to upgrade its shock-absorbing system.
What are #3 Hybrid’s strengths?
It is an eye-catching model from an aesthetic point of view, especially the upper. Moreover, the sole with the window, conceived to see contrasting colours, gives a bold touch; at the same time, another added value is the sole’s softness, a strategic trait communication-wise because it is easily conveyed to the clientele. The thorough use of polyurethane entails a significant benefit compared to other solutions with inserts made in different materials used by plenty of our competitors, especially when it comes to safety shoes worn for over eight hours a day and in peculiar environments, where the abrasion is constant.
Design-wise, what kind of R&D activities do you carry out?
Every line, before its launch on the market, goes through a study phase, that may last one or even two years. Starting with the outline of the project to the design stage, up to the selection of materials; then, when we have the first pilot moulds, we proceed with the injection to verify if everything is under control. After that, for a couple of months, we have the shoes tested in-house, so as to make any further adjustment and, only when we are sure that there are no issues, we kick off the actual production.
According to market demands, what is your stance on certifications?
All our products are certified, the latter a pivotal aspect, widely praised by the customers. Bearing this in mind, GIASCO’s partner is Ricotest, a firm based in Pastrengo (Verona province), in the Garda Lake area, whom we deem the best on the market. Given that ours is a technical product, in addition to the traditional certifications that we already have, we always strive to grasp the latest market demands from our customers and, together with them, we look for other certifications that can meet the end users’ satisfaction so as to stand out in specific sectors. We carefully pay heed to the suggestions of our clientele worldwide and, often, we manage to keep a step ahead of times.
What is the relation between your company and the local territory?
For several decades, the Chiampo Valley, the cradle of this sector since the beginning, has been acknowledged as one of the world’s most prominent leather processing clusters, boasting a skilful combination between a long-standing technical craft know-how, entrepreneurship, and a forward- looking attitude. Thanks to the development of this district, the territory houses several excellent specialized technical institutes that provide companies with highly qualified human resources: both aspects play a key role for the production of safety footwear.
What are the main benefits of belonging to the Arzignano district?
It means to receive daily supplies of the best materials in terms of resistance, elegance, smoothness, waterproofing and breathability: for instance, we turn to a tannery nearby to purchase leather, each week our technicians go there to check the quality of the materials. For the rest, all our manufacturers are Italian, whereas, when it comes to moulds and small metal parts, we rely on Veneto-based firms.
Last but not least, can you tell us about your commitment sustainability-wise?
We are constantly on the lookout for low-impact products. When it comes to both hides and synthetic materials, we pick those that can ensure a higher degree of environmental safeguard. Among the various projects in progress concerning production, we are testing various percentages of recycled polyurethanes in the sole, able, in turn, to be re-introduced in the processing cycle. Fully aware that sustainability will be a key factor in the upcoming future as well, the corporate goal goes beyond the sole economic result. For this reason, by adding Corporate Social Responsibility to our mission, we are committed to ensure the utmost social protection and concrete environmental safeguard.
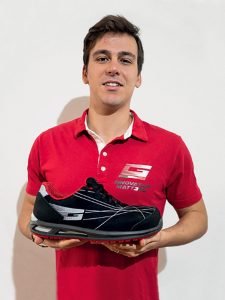
Ettore Caneva Resp. Marketing e R&D