Gusbi, a market leader in the production of polyurethane soles and footwear equipment, looks to the future and promotes more sustainable practices and superior customer service.
The word “sustainability,” of high inherent value and sometimes overused, has been interpreted differently over the years. Today, sustainability is understood as the place where economy, social realities and environmental health are intertwined. Irene Bianchi, Gusbi S.p.A.’s Planning and Control Manager, shares with us her perspective, which is to combine in an increasingly effective and deep-rooted way, its own skills with highly innovative and sustainable, technologies, because the key to remaining competitive is to continue to invest on the constant updating of its know-how to meet new needs the market.
What are the projects you are currently working on?
“The technology of our machines is evolving on a daily basis. What can be integrated, to improve the operation of our machinery, are electronics and robotics. Each of our machines, compared to previous versions, is constantly evolving, especially in recent years where we have focused a lot on the environmental factor. Thanks also to the raw material processed by our machines, namely polyurethane, today we are able to create a product with a fairly high percentage of recycled material. Our technology, which actually started many, many years ago, has been repurposed by mixing polyurethane with sole remnants or upper off-cuts. Basically, what do we do? All the discards we get are shredded into very small pieces and then mixed inside the new soles, thus creating a true circularity of waste materials. This process is another step in building a true policy of respect for the environment.”
In pursuit of greater sustainability, is this the new mantra?
“Actually, the nice thing is that Gusbi was already ready to meet this kind of demand because this technology, which is used to blending polyurethane with raw material waste, and has been used for a long time to make polyurethane soles blended with cork. So the product is already there and, today, we can also guarantee the same quality and performance on this type of sole as well. Nothing new has been discovered: we work on the basis of an already existing technology, repurposed in another way.”
As part of this green evolution, have you also embarked on a path of decarbonization?
“Our company, being associated with Ascom, is constantly working to maintain its green license plate. Some European countries, such as Spain and Portugal, for example, require us to have this particular certification, which certifies the precise calculation of the carbon footprint, so that they can communicate to the end customer what the consumption is to produce a pair of soles or a pair of shoes.”
What does the market recognize most about you today?
“Our history, our know-how. Gusbi was established back in 1946, when polyurethane did not yet exist. When people started using this material to produce soles in the 1970s, we grew with it. We were the first to process this material and have never abandoned it. We possess a unique specialization that thus allows us to enter different sectors. So not only footwear, but also filters, bicycles, stroller wheels and more. Over time, we also had the opportunity to create a proper archive of all the machine outlines from the 1980s onward. This allows us to ensure timely service even for those who have somewhat older machines.”
For Gusbi, customer service has always been a fundamental component….
“For years, Gusbi has relied on local teams in all continents, trained directly in the company, which offer support to our customers around the world. This service has always been highly appreciated, especially during the past two years when it was not possible to travel: even on that occasion, in fact, we were able to ensure the usual installation and assistance services right on site.”
There is a lot of talk about reshoring, about returning production to Italy because of labor shortages. We know that labor has a huge impact on the final cost of products. How does Gusbi address this problem?
“Eliminating the man is neither possible nor imaginable. What needs to be done is to redirect the operator. For example, on our machines normally five operators have to work and be responsible for extracting the soles and spraying the release agent. Thanks to our collaboration of more than 20 years with the company Autech Toscana, we have been able to replace them with robotics. But this has not meant eliminating the human contribution. What is necessary is to have the operators’ skills change, to be more specific with respect to the use of modern technology and installed electronics. This is about retraining not elimination.”
Last question: how do the technologies you bring to your machinery come about?
“The secret is to listen very carefully to customer needs. Gusbi works nonstop on improving and customizing its machines so as to meet all the various demands and needs in a timely and fast manner.”
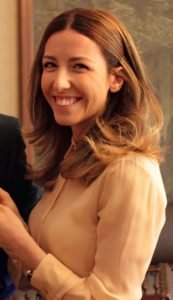
Irene Bianchi, Gusbi S.p.A.’s Planning and Control Manager