i-Tech is investing in the tanning sector’s future with 4.0 solutions for production efficiency, designed to improve the working environment as well as to reduce waste sources
To actively contribute to the production process efficiency in the tanning industry with 4.0 solutions. This is the latest mission pursued by i-Tech, company based in Sassuolo, Modena province, that for over twenty years has provided an ample range of technologies and machines, used in several sectors, for the making of varnishes, inks, dyestuffs and paints for both traditional and digital (dosing tinting systems) decorations. The Emilian firm is currently experiencing a period of consolidation and of further expansion thanks to the resources invested in the last three years, a pivotal decision that has helped it gain a foothold in the leather finishing sector with a new, unique identity. Bruno Bettelli, President & CEO, and Andrea Carandini, Sales Director as well as sector manager, outlined the keystones at the core of i-Tech’s business strategy.
What can you tell us about the new identity chosen to deal with the tanning sector?
B.B. In places where we initially acted as machinery manufacturers and suppliers, now we are acknowledged as developers of complex solutions aimed at providing information and data – clear, well-structured, user-friendly –, so as to be fully aware of the level of efficiency reached.
Quantity-oriented manufacturing is no longer the sole objective: the tannery of the future must be sustainable, with a low environmental impact, able to reduce both waste and washing wastewater. Our mission lies in finding production efficiency solutions fully compliant with the Industry 4.0 standards and with the Lean Manufacturing principles. First of all, we look for waste and inefficiency issues and, secondly, we proceed with a redefinition of the production process, resulting in the installation of machines and software programmes designed to monitor and manage said process by upgrading its efficiency rate and its functioning.
Via our change in market placement, we have strived to provide the customers with tools for the implementation of integrated solutions, a decision that goes hand in hand with the promotion of a new eco-friendly culture applied to the processing cycle. Because, after all, the toughest part does not concern the adjustment of the machine layout to a specific space, but – once the system has been manufactured, supplied, installed and powered up – it regards the ability to foster a shift in mentality when it comes to manufacturing procedures. In our case, it means ensuring the implementation of a Pull system, rather than a Push one, that is, we must guarantee that the product releases are in line with the actual needs, so as to decrease overproduction as well as to avoid underproduction.
So, we can call it responsible innovation, right?
B.B. Professionals and firms engaged in this sector must be able to skilfully combine innovation with environmental as well as social sustainability. We cannot jeopardize i-Tech’s mission, that is, to improve in a steady, significant way our customers’ working conditions and environment.
Automation plays a pivotal role when it comes to the reduction of the product’s impact on the employees, thus sparing them any repetitive, exhausting, harmful activity, on the environment, so as to avoid waste and unnecessary washing procedures that damage the purification systems, and on the citizens as well.
Are you already reaping the benefits of this change of route?
A.C. We have set off on a path together with prominent tanneries, a feat that is helping strengthen the sector’s trust in us. The subsidiary companies of high-end fashion and luxury brands have turned to i-Tech, preferring our firm over other competitors, because they have noticed our added value: the factors that really make the difference are not merely the upgrading and the price, but rather the closeness of a partner who can support the tannery throughout an evolution process focused on responsible, low-impact production, the latter a pivotal element in order to gain the customer’s favour.
Reputation is a keyword, a concept we have always insisted on: what we have achieved lately manages to further consolidate a reputation built during twentysix years in the business. The philosophy at the core of our growth, first in the ceramic sector and later in the packaging field (development of inks for printing on flexible packaging solutions, either in film or cardboard), is the same one we have applied to the tanning industry: to keep the Brand Promise in order to win over the clientele’s trust and to strengthen our market reputation.
What has the diversification of application sectors entailed for the company?
B.B. The change concerning the application and use of our systems has resulted in construction materials research. From 2014, thanks to a project in collaboration with the University of Modena and Reggio Emilia, Materials Engineering department, and with the Jaume I University, Spain, we have acquired a solid know-how materials-wise, concepts that have helped us deal with the new sector. We studied thoroughly the tanning finishing cycle prior to our involvement and, in 2020, we filed the first process innovation patent (followed by four more), thus simplifying and streamlining the workflow.
In the past, R&D investments accounted for 12% of the turnover; for about four years now, the resources have been distributed between product/process innovation, strategic marketing and human resources training.
As for product customization, do you provide daring solutions?
A.C. Customers show a strong interest in co-design: together with them, we manufacture solutions tailored to one’s specific needs, with a customization percentage reaching 85%. A decision that entails attention to detail, passion and top-notch skills, that is, features embodied by craftsmanship. We meet individual demands, much to the clientele’s satisfaction.
How do you deal with the lack of qualified technicians able to implement digital equipment to support enterprises?
B.B. We train the resources we hire and, at the same time, we take the responsibility of guiding the employees lacking the skills and cultural background required to manage an advanced system. Not only do we supply the machine, but we also give to customers the right know-how to use it in a proficient way, standing by their side as long as necessary. This process features three steps: the installation of an integrated plant compliant with the Industry 4.0 standards; the implementation of predictive models, so as to activate product releases only when the application machine needs them; the commitment to develop and provide, with a long-term prospect, AI systems. The customer demands solutions, not products. This is our approach.
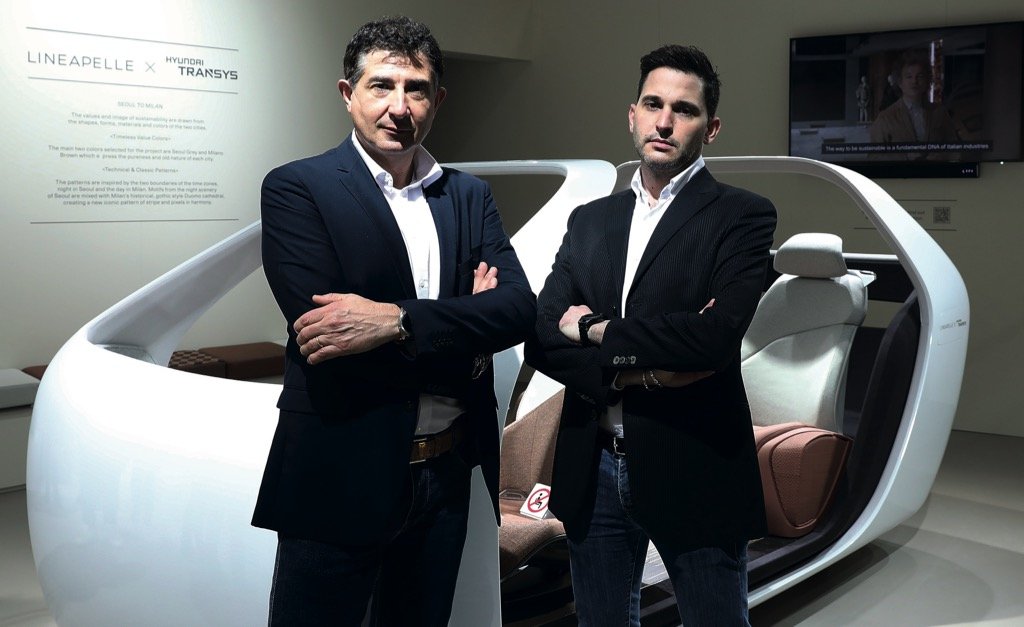
i-Tech’s management at the latest edition of Lineapelle: from the left, Bruno Bettelli, President & CEO, and Andrea Carandini, Sales Director