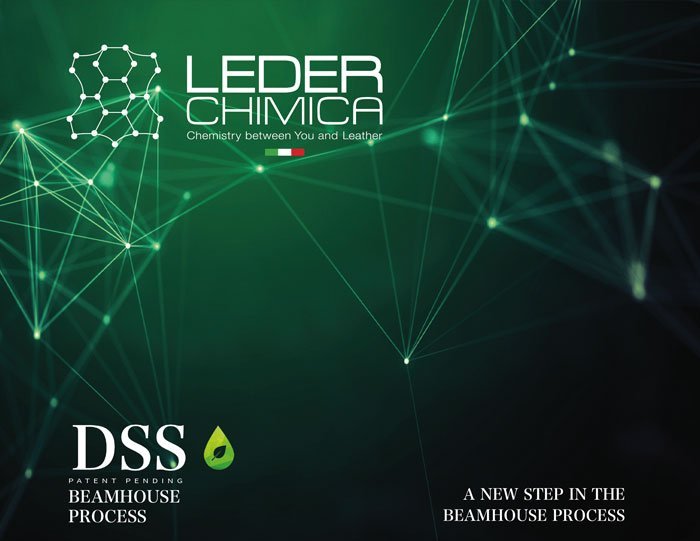
Leder Chimica, based in Arzignano (Vicenza province), has developed two important procedures, one, the DSS, related to the liming process, the other, SSP3, to the tanning one. Both improve leather quality and reduce environmental impact during the whole cycle
Michele Zanconato, together with his two sons Enrico and Filippo
Leder Chimica invests and focuses on high technology to overcome the future challenges in the tanning sector, both at an Italian and international level. For 35 years, the company, founded in 1986 by Gastone Zanconato and now led by his son Michele and grandchildren Enrico and Filippo, has been a reference point in the development and production of chemical products for leather destined to different sectors, such as that of clothing, furniture, footwear, automotive upholstery and interiors, leatherware. In recent years, the Venetian company has grown a lot, thanks to its guaranteed technical assistance, but above all to the investments in increasingly innovative and environmentally friendly products. This is an attitude that the Vicenza-based company has always pursued: unceasing R&D activities to offer the market high-performance products. Its longexperienced staff also offers a timely intervention according to the customers’ innovative requests.
The latest innovation launched by Leder Chimica is a sustainable technology, developed to improve the standard liming process in terms of reduction and elimination of highly polluting substances, without sulphides and sulphhydrates, able to keep a very high leather quality and taking care of the production KPI during the entire process within 24 hours. Several tests during production have proved the efficiency and versatility of its application, on all types of raw material regardless of conservation methods. In particular, the company has launched the DSS technology for the beamhouse which, combined with the equally innovative SSP3 tanning process (that we’ll report in-depth in the following editions), guarantees high quality and the absence of polluting components.
On the right, a crust processed in the traditional beamhouse; on the left that processed with DSS
“What we have called DSS – explained Filippo – is a new liming process, for which a patent has been applied for. The purpose of our DSS technology is to provide a better performance in opening and relaxing the internal structure of the fiber, as well as a perfect hair removal; the final effect is a completely clean surface compared to the natural pigment of the raw material, to be used in several final destinations of excellence such as Nubuck, Aniline and Semi- Aniline. Moreover, wastewaters are free from harmful and toxic substances and can therefore be exploited in other sectors without necessarily destined to the waste water treatment plant.
How was the project conceived? Similar processes already existed: they consisted of a selective system through the use of hydrogen peroxide, but this raw material is actually very complicated to manage as it does not remain stable over time. However, ours is an oxidative process without H202, so there is no danger in storage procedures and, above all, it keeps its potential over time. The project, developed in our in-house R&D laboratory, came from the need to have a sustainable product. The qualitative benefit is that it leaves the grain intact, eliminating remaining hair inside the bulb and leaving no residual pigmentation or blood spots. One of the advantages of this oxidative process, is that the protective effect from molds is prolonged in the storage phase.
What are the main features in the production process? This process doesn’t require any need for lime nor sulphide during hair removal – explained Michele – and it also guarantees a wider choice thanks to its much whiter color than the one obtained through a standard process. This feature is essential for those tanneries that produce high quality articles with very specific requirements for color gradations: an undeniable advantage for the tannery which thus has a raw material suitable for multiple uses.
And what are the environmental benefits? From the point of view of sustainability, thanks to our process, the use of sulphide and sulfhydrate during hair removal is eliminated, also lowering the PPM values in wastewater, thus favoring a much safer work environment, free of bad odors and volatile gases as dangerous as H2S during the de-liming and pickeling phase. Our studies suggest that the waste baths of our process have a high protein content, free from harmful substances and can therefore be exploited in other sectors, without necessarily being destined for the waste water disposal system.
So, what are the main prerogatives for those who use the technologies you launched on the market? Surely, the advantages in terms of eco-sustainability are the most noteworthy; as mentioned, it is a process that does not make use of sulphides, sulfhydrates or lime. From the qualitative point of view, the DSS reaches very high standards, and guarantees dyeing uniformity on the constellation and on the wrinkle of the leather. Finally, this method also allows the 24-hours-a-day beamhouse process, offering significant production advantages especially in the case of large factories.
www.lederchimica.com
Another important result achieved by Leder Chimica concerns the SSP3 tanning process which, as Michele Zanconato and his sons Enrico and Filippo explained, is meant for the production of completely metal-free and glutaldehyde-free wet white hides, guaranteeing an excellent white pick. This method offers infinite coloring possibilities as well as excellent heat resistance, thus allowing processing with release paper machines or bycast systems.
Leader Chimica is looking for new agents in order to widen its sales network.