Wintech and Exena enter into their first collaboration to tackle together essential issues such as development and growth.
Technological revolution and business are now at the center of any self-respecting industrial activity. In the last thirty years the world as we knew it has totally changed and the introduction of new systems and innovations developed on several levels have progressively entered and influenced the lives of everyone, including that of consumers, who have become increasingly demanding, especially when it comes to quality, safety and health. Exena, a group based in Civitanova Marche, market leader in technical-safety professional footwear, and Wintech, a Venetian company, reference point in the production of injection machinery for the footwear industry, join forces to meet the demands of an ever-changing market and to grow through valuable relationships and a win-win approach to business. To fully understand the motivations and goals behind this new partnership, Alfio Cicchinè, CEO of Exena, and Paolo Miotto, flanked by his son Andrea, Founder and North America & EU Sales Manager of Wintech, gave us an interesting three-voice interview underlining how much experience, competence and trust can be essential in order to evolve.
Mr. Cicchinè, why did you choose Wintech?
“Our company manufactures many different products in the safety footwear sector and we are a renowned brand thanks to our high production quality, innovation and flexibility. What let us stand out among others are the constant research and design on a product that is not easy to appeal, our customer care service, our flexibility and our excellent quality/price ratio. But all this is not enough to respond to increasingly competitive requests. Our wide offer was only lacking of boots, so we looked for a machine that was able to work a difficult material such as polyurethane. We have known Wintech for some time because it was already one of our suppliers of PVC processing machinery and we literally trusted their word and their experience. This purchase is finally allowing us to produce 100% Made in Italy products – our production, until now, has always been mainly located abroad. At the moment we are one of those very few companies that produce polyurethane footwear, but we are confident that the dynamism of our sector, in constant search for news, will respond very well to this type of product.”
Why are you sure that polyurethane will have a great development?
“I am convinced that we will see very rapid growth if the product is launched in the right markets such as Northern Europe or Germany, just to give an example, where this type of product is already widely used. Our intention is to present our new polyurethane boots at the next fairs in Paris and Düsseldorf. Up to now we have only thought about learning how to do it in the best possible way because quality is one of our main focuses and we’ve been always renowned for that.”
Quality at all levels…
“Exactly. We produce about 2 million pairs of shoes a year and we register a return figure of 1%, which is really negligible. If this is not a prove of quality, what is it? We never saved on materials: we learned this from the beginning, when we started collaborating with the most important sports and safety footwear brands on the international market. We are used to working at very high levels and, over the years, we have achieved the most important international certifications.”
How important is the Made in Italy label for you today?
“It is very important; our latest investments prove it. By 2024 we plan to reach 40% of our turnover under the “Made in Italy” brand. We can affirm that, considering that we are already able to ensure fast deliveries to our customers, we will be able to have our shoes on their feet the same day.”
How do you manage to guarantee such fast deliveries? “Thanks to the capacity of our warehouses which contain 350/400 thousand pairs of shoes in stock, immediately available to be delivered all over the world, and to the automation of logistics which represents a decisive strategic choice for improving the competitiveness of our company. We also keep on working on our facilities’ enlargement: we have recently opened two new offices, one in Canosa and one in Ascoli Piceno, where we have installed two new cutting-edge machinery.”
At the same time, Wintech’s corporate philosophy also focuses on the relationship of trust and close collaboration with its customers to best meet their specific needs. As a matter of fact, all the machines are designed and built entirely in Italy, within their own headquarters in Mellaredo di Pianiga. Furthermore, Wintech not only has specific skills to create targeted solutions, but has always had the integrated tools necessary to implement them.
The collaboration with Exena thus endorse the implementation of a new winning business model based on sharing and offering companies customized solutions that add real value to the customer.
“We are delighted with this prestigious partnership. Working with an internationally renowned top player like Exena was a great opportunity that we were happy to grasp,” declared Paolo and Andrea Miotto. “Initially the project started with the sole supply of a machine to process PVC, an area in which we have developed a forty-year experience that allows us to be appreciated worldwide according to the level, specialty and performance. Along the way, Exena needed a machine also for PU boots. Thanks to the trust placed in us, we have taken up their challenge to carry out a n all-round project, providing machinery, the design of the boot and the construction of the molds, the latter made under the JuniorTech brand, which are guaranteeing excellent results and high performance.”
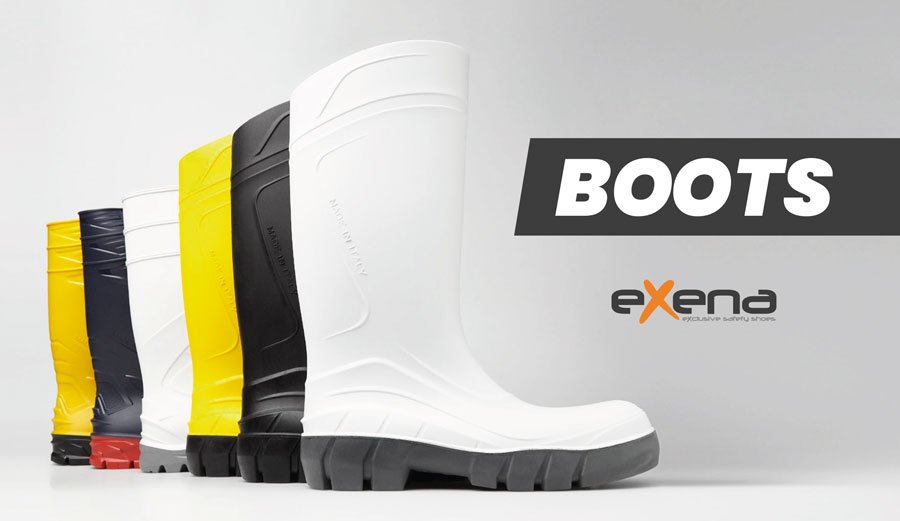
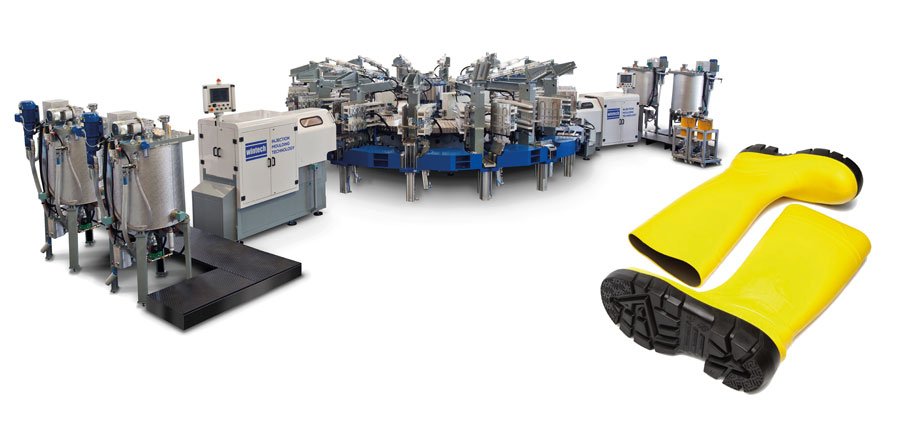
WF – a machine for the production of polyurethane boots. This material is extremely soft and elastic even at very low temperatures and guarantees excellent thermal insulation and very high mechanical resistance

WLX – a machine for the production of PVC boots, made with an antistatic compound enriched with 9% of Nitrile Rubber both for sole and upper, which ensures a particular softness of the material in order to offer the best resistance