SC Costruzioni Meccaniche, based in Empoli (Florence, Italy) and specialized in the production of tanning machines and purification plants, looks forward to the year that has just begun to grow on the Italian and foreign markets.
“After the two-year period 2020-2021 characterized by the pandemic, last year we recovered very well, returning to pre-Covid levels, with turnover registering an increase compared to 2019”. With these words the two owners and partners, Roberto Calattini and Fabio Scardigli, explains the scenario concerning SC Costruzioni Meccaniche of Empoli (Florence), which are present on the Italian and foreign market since the mid-1980s, which designs, builds and installs plants and auxiliary equipment for various industrial sectors, especially tanning machines and purification plants.
“The performance recorded in 2022 – to which the two entrepreneurs of the Tuscan company specified – was favored by a series of factors, in particular by having launched innovative products on the domestic and foreign markets, but also by having managed to penetrate new markets. In Italy have certainly helped and influenced the concessions linked to Industry 4.0, which arrived when we were already ready for an important phase of relaunch, but which undoubtedly guaranteed us a good boost”.
What were the new products in the second half of last year, also in view of 2023?
“In reality there have been no substantial innovations, we have designed and built a stamping press with two trolleys for a customer, confirming our ability to customize part of our products according to needs. For the rest we have continued with the policy of constant updates, especially as regards automation, also in this case the boost from Industry 4.0 was important. The growth in the cost of raw materials, characterized by an anomalous trend during the year, also weighed on the final accounts for 2022. Example in the American continent as a whole, from north to south, it must be noted. Thanks to the dollar/euro exchange rate, they have suffered less from the price increase”.
Speaking of foreign markets, what can you tell us about the current scenario?
“We returned to China after almost 3 years, in autumn of 2022, confirming a slowdown that affected a large part of the Asian continent. An area where the economic recovery is evident is South America, in many of these countries people work for the automotive industry, so we are in the heart of the tanning industry. Also in Mexico there is a lot to be done, almost all the companies are already present in that state, which is no longer a novelty to discover. We have been following all these markets for decades, we started going there in 1995, so we know them very well and know how to work, even if the goal is always to penetrate and expand further”.
What are your strengths abroad?
“Wherever we are able to guarantee assistance, in every country we have contacts who are important points of support, but almost all of our customers are able to get by. In many tanneries in South America there are internal mechanics, who sometimes they contact us by phone especially with regard to software and we are able to help them remotely. We must also say that our machines are very performing and rarely need intervention”.
Another topic is linked to an ever-greater attention to the environment and to certifications…
“For some years we have joined the “Targa Verde”(Green Plate) initiative of Assomac, the hope is that interest will grow over time, for that we are ready. All S.C. Costruzioni Meccaniche machinery is certified according to current regulations, all of which represents a guarantee for our customers but also an important calling card. Compared to the competition, we also have the 10.90 Certification which, however, does not specifically concern the tannery sector, but rather welding and the construction sector. Thus, when there is the need to install some plants, especially on third-party projects, we are sure to comply with the regulations”.
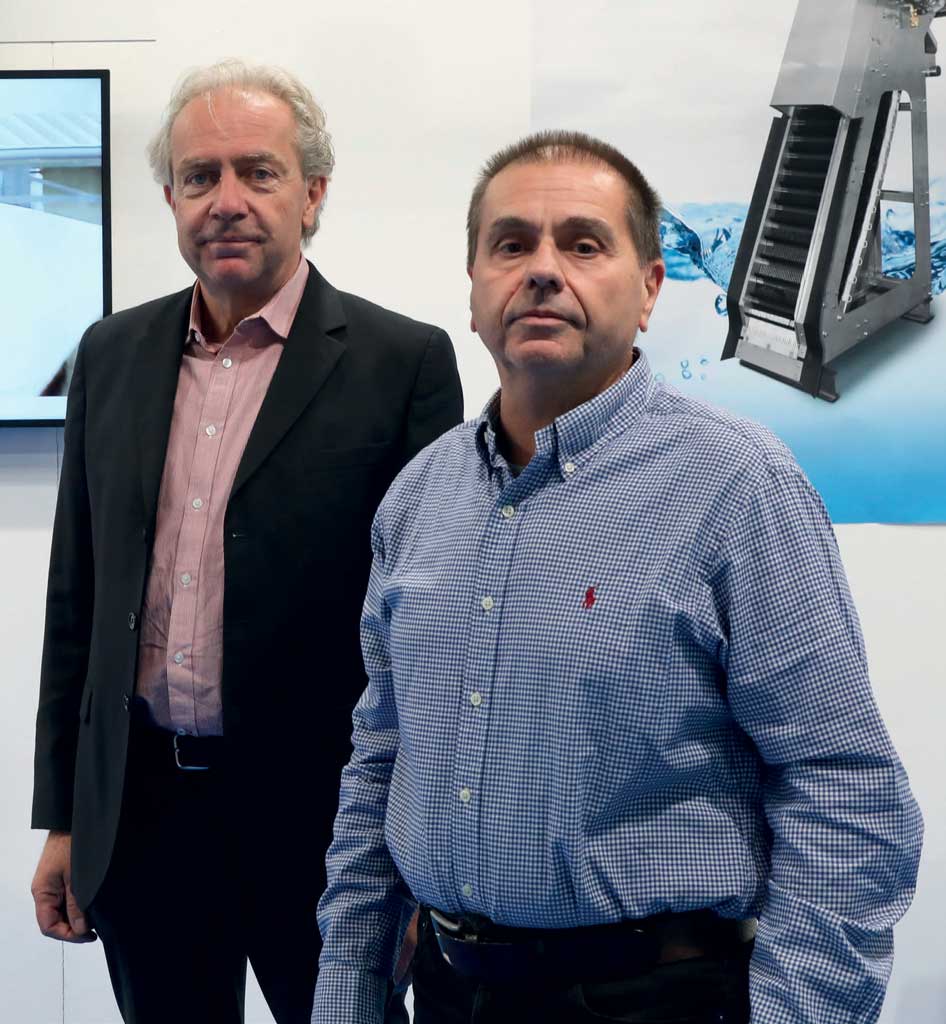
Roberto Calattini, at the head of the company together with the partner Fabio Scardigli
The machine, covered by a customized patent, represents one of the tops of the range signed by S.C. Costruzioni Meccaniche
The Hairpress filter is a self-cleaning machine specially projected for hair recovery in liming and can also be used for filtering other kinds of leather tanning industry emissions or emissions of other industrial processing. The main characteristic of the Hairpress filter is that of dewatering and compacting the retained material thanks to a system consisting of a rubber cone with a peculiar shape (S.C. patent) that causes a volume reduction and therefore a reduction in the costs of waste disposal.
We asked the two partners Roberto Calattini and Fabio Scardigli to list the technical features of this machine. “The Hairpress filter – they said – consist of a filtering pipe with semicircular section, structured in very thick stainless steel perforated plate, with a screw scraping the inner surface of the pipe. The material retained by the filtering panel is removed by the screw and driven to pass through the rubber cone where, thanks to the developed pressure, it loses most of retained water. Special brushes on the external side of the screw deeply clean the filtering holes and prevent them from clogging. Then the filtering flow rate is always high and the filtering system maintenance is reduced to the lowest levels. The filter is always equipped with an inner immersion pump, for recycling the filtered liming. Electrical board and control panel are placed on the machine edge.” The main feature of this machine is the hair recovery from liming baths. “The non-destructive systems of liming – add the owners – enable a high reduction in the polluting tanning waste materials both for COD (30-50%) and for suspended solids particles (40-60%), ammonia and sulphide. This processing is effective and easily manageable, provided that the waste disposal flow rate of the filtering system is adequate, so that carrying out times can be reduced. The Hairpress filters are characterised by a high treatment flow rate and by simple functioning and installing, that make them adaptable for any situation. The machine can be gravity fed if the drums are placed about 100 – 200 cm from ground or by means of pumping in case of lower height. In both cases the liming is discharged from the drum throughout waste valves, collected by semicircular gutters (S.C. supply) and conveyed to the filter directly or by means of an immersion pump. The filtered liming is re-pumped to the same drum by the inner pump. This processing lasts till the complete hair removal from liming (about 1 hour). The retained hair is compacted and discharged with a residual humidity of 40-50%. The same machine can serve several drums in sequence and the hydraulic circuit of drum selection in recycle ca be equipped with manual or automatized valves or with servo-controlled valves.”
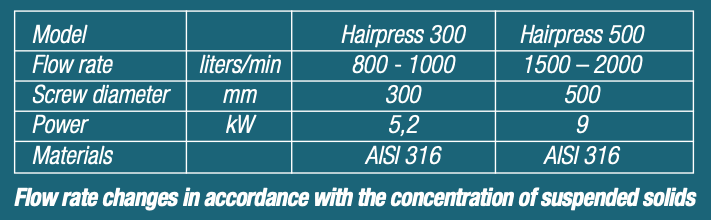