Renewable raw materials, recycled plastic, Hot Melt technology ensuring zero solvent emissions, solar panels supplying 400 kW. These are the main premises lying at the core of the success of Tecnogi, leading enterprise in the production of materials for toepuffs, counters and reinforcements to be used in the footwear sector.
Over the years, the firm headquartered in Borgolavezzaro has experienced a steady expansion, resulting in a global sales network encompassing more than 70 countries worldwide as well as in the establishment of several subsidiary as well as associated companies (that is, Tecnogi Jasmine, Tecnogi Plast, Tecnogi India and Sipol), in order to integrate both the upstream and downstream segments of its core business.
At the latest edition of Lineapelle, Tecnogi confirmed its commitment to sustainability: the managing director Gianni Zanetti explained the firm’s strategies in favour of an eco-friendly economy, thanks to investments in renewable energy sources and to the production of low-impact articles – a mission constantly pursued, yet never put in the limelight.
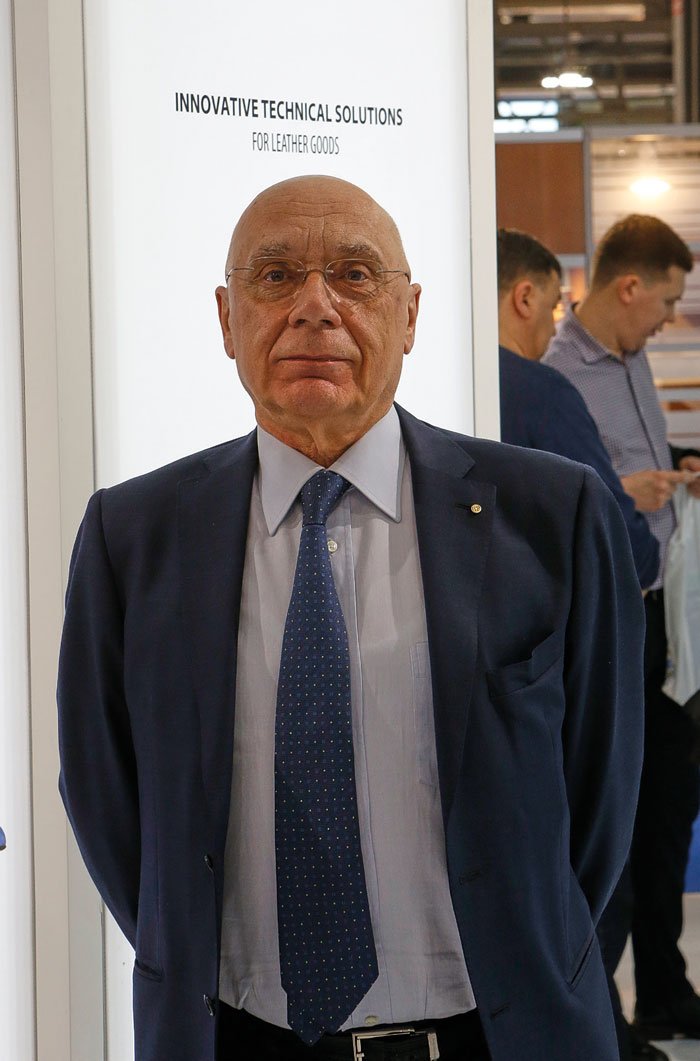
Gianni Zanetti, Tecnogi’s managing director, at the corporate stand during the latest edition of Lineapelle.
Why can Tecnogi be described as a “green company”?
The protection of the ecosystem is now acknowledged as an ethical value as well as a strategic priority by the majority of companies: nevertheless, in order to effectively put into practice one’s environmental policy, it is required a well-established expertise. It is a pivotal step. For over fifteen years, Tecnogi has been paying close attention to environmental safeguard, thus pursuing a strategy aimed at the production of eco-friendly materials. The shift to sustainable manufacturing systems is a challenge that involves ideally the entire society, since nobody wants to live in a heavily polluted world. However, when it comes to articles made with recycled materials, the common thought is that they are qualitatively inferior to those produced with virgin one, and thus they should cost less. The true “green” philosophy, on the other hand, should not cause problems for companies, but help those who invest in this field to have an economic return. Each firm develops its eco-friendly strategy according to its own expertise, beliefs and goals. We have chosen the “no waste” philosophy, that is, we recover waste by-products, turning them into raw materials. Its main strength lies in the ability to boost a circular economy that can combine ecology and profit: if I manage to manufacture “zero-waste” goods, thus successfully re-using all the waste material, this procedure will result not only in the marked decrease in the environmental impact, but also in the fostering of a virtuous economy for my enterprise.
What are the main features of Tecnogi’s products?
We have been the pioneers in the recovery of the by-products of our own processing cycle as well as of those of selected customers. Ten or so years ago, we invested 1 million euros in order to implement an innovative change to our first co-extrusion line so as to be able to use salvaged materials. We have then developed new articles containing a percentage of recycled materials ranging from 50 to 100%, distributed on the market at the same price as the products made with virgin ones, featuring the very same mechanical performances and application characteristics. I am very proud of this endeavour as well as of the positive results we have achieved, both in terms of quality standards and of economic return.
Why have you chosen the Hot Melt technology?
The development of the Hot Melt technology has allowed us to produce in-house hot melt adhesives, completely devoid of any solvent and perfectly fitting our processing system, thus thoroughly eliminating any hazardous emission in the atmosphere.
What are the main challenges for the upcoming future?
The laboratory represents the first step towards the outlining of the corporate mission. Our R&D activity aims at improving products featuring highly innovative characteristics and contents. The true challenge for the future lies in the development and experimentation of new line of eco-friendly, entirely recyclable products, manufactured with raw materials derived from renewable sources.
This attitude has led to the launch of Biorel, a thermoplastic material for counters, made by transforming polymers from renewable sources: in their chains, natural starches were inserted so as to ensure their complete biodegradability.
Biorel has been certified as biodegradable and compostable by the OWS Institute based in Ghent, Belgium, since it is fully compliant with the requirements set by the international regulations EN 13432 and ASTM D 6400. After 60 days spent in humus similar to the one used in the landfill, Biorel’s weight loss amounts approximately to 87%.
Is the installation of solar panels part of the corporate investments for a sustainable development?
We are pioneers in the production of clean energy as well, thus further confirming our commitment in terms of environmental safeguard. A photovoltaic plant featuring a 400 kW power capacity has been active since June 2011 and it meets approximately 25% of our energy requirements. www.tecnogi.com