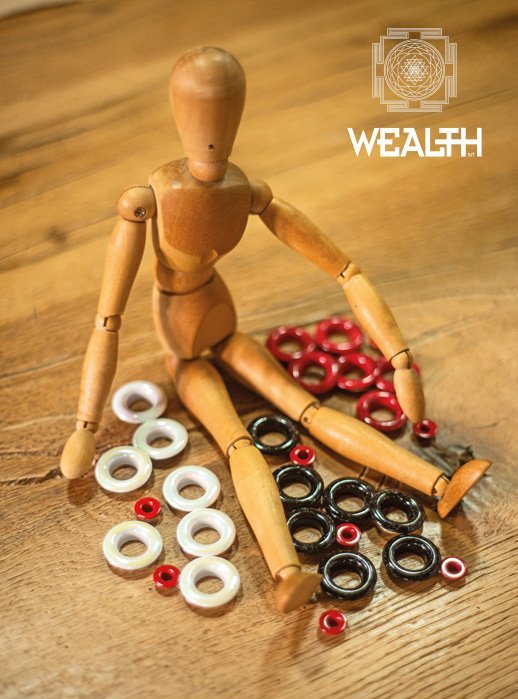
Wealth has been the perfect wingman for big and haute-couture brands for years: it is the partner who always has the solution at the right time, the one you can count on for a job well done and, if needed, done at the speed of light.
When you know you’re good at something, the smartest thing to do is to invest in your value. Your own reputation will then open doors for you, without having to knock. This is, in brief, the parable of Wealth, a Desio (Mi) based company that deals with the supply of small metal parts and accessories for the footwear, clothing and leather goods industry. We spoke with Andrea Patria, owner of the company, after the difficult months marked by the Coronavirus, to understand if and what has changed in the world of fashion supplies, but also for the sheer pleasure of looking behind the veil of an all-Italian success story.
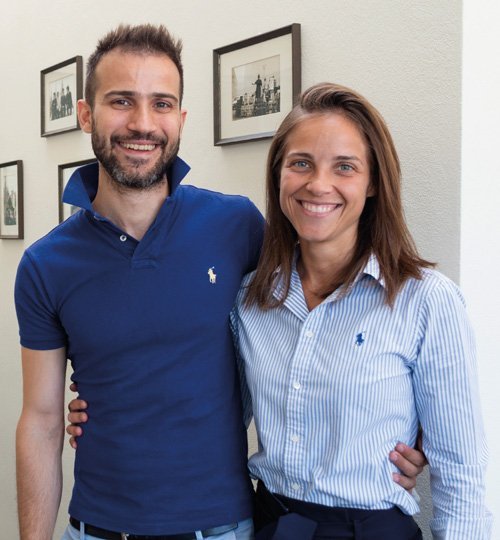
Andrea e Chiara Patria
How did you “become” Wealth, an Italian excellence in the sector of small metal parts supplies for the fashion industry?
We were born with the production of technical articles, a residual sector for us today. The relationship with the fashion industry was born naturally and we found our place in the industry thanks also to the fact that fashion itself has increased its demands: today, big brands want small parts to be more resistant to oxidation and atmospheric agents, and to have particular finishes, demands have increasingly specialized and we have specialized in fulfilling them. We have focused on customer management, our job is, ultimately, to solve problems: we follow the entire production process and we often have to run here and there just for a sample, big brands need immediate responses and actions and we stand out for the speed of our work. It is also essential to have a well-stocked warehouse: we stock prototypes and articles in many galvanic finishes for each customer and this often helps us – and helps them – to solve problems quickly.
Do you follow the production of small parts since their conception?
Most of the time we deal with the industrialization of a customer’s idea, its adaptation to large-scale production and its application on different materials. We have an internal technical office and during the production phase we also rely on the specialized technicians of our subcontractors. We are always the customer’s interlocutor: we take care of printing raw items, making quality checks on them, follow the varnishing phase and the whole process up to the final packaging.
The relationship with subcontractors must be of fundamental importance for you…
Yes, and in fact our subcontractors are almost always the same, historical and trusted. We have set up a functioning supply chain and we are committed to maintaining it. For traditional processing we use companies from Milan and Bergamo, while for frame processing we go to Tuscany, where they are specialized in this specific processing.
How did you face the production crisis caused by the Coronavirus epidemic?
We’ve been watching the situation: we have reduced costs by optimizing the warehouse and lowering its value, eliminating material that had been standing still for a while. The amount of work has decreased, now it’s starting to grow again and we are confident that in autumn we’ll see a rise in the volume of orders. Our customers have shown the tendency to stick to the classics, items and styles that have brought numbers in previous seasons. There is a reluctance to invest, to try new things.
You’ve made a large investment in automated warehouses. How do they allow you to stand out?
The automatic warehouse allows us to be very fast in the preparation and fulfillment of orders and above all it enables us to have an extremely reliable stock. We have two automatic warehouses, one for raw products and one for semi-finished and finished products; we use two other smaller warehouses for sample archiving.
Sustainability of production and demand for metal-free items: how much do they impact on your business?
Our subcontractors over time have adapted to environmental directives, big brands are very attentive to this issue and they can send inspectors to check the quality of waters and other parameters. As far as metal-free is concerned, we also work with Abs and we do research on new materials, there is demand but for the moment we cannot speak of a real trend. It’s still complicated to overcome some technical issues, small metal parts offer quality standards that for the moment aren’t matched by total metal-free items.
www.wealth.it