The upgrading of existing machines is currently acknowledged as a valuable alternative to the purchase of a new leather painting plant, as the latter is usually very expensive. This solution has been put forward by SPRAYTECH, firm headquartered in Lonigo (Vicenza province) that designs and manufacturers systems and accessories for industrial painting; besides that, it also deals with the making of special plants and automations for both the domestic and the international market. Relying on more than thirty years of experience in the business, the Veneto-based enterprise has always stood out for its commitment to provide the clientele with cutting-edge solutions. As a matter of fact, in addition to the production of painting lines equipped with state-ofthe- art technologies, SPRAYTECH offers another option to customers who do not wish to shoulder substantial investments, that is, the revamping of existing machines. In the Lonigo-based headquarters, we met Mauro Golin and Marco Zampieri, respectively business partner and general manager: they explained the corporate strategies and their high expectations, especially in terms of feedback from the international markets (currently, the exports account for a 60% share of the turnover, but it will further grow in the upcoming years). “The tanning sector is going through a phase of uncertainty on a global scale,” stated Golin and Zampieri, “for this reason, several entrepreneurs often think twice before tackling significant investments, that can amount to 1 million euro and sometimes even more. In view of the lack of disposable income, we have chosen to provide another option, that is, the upgrading of the existing plants, by changing either partly or completely the technology and by adding new components, in order to guarantee more efficient, qualitatively superior performances compared to the previous ones.”
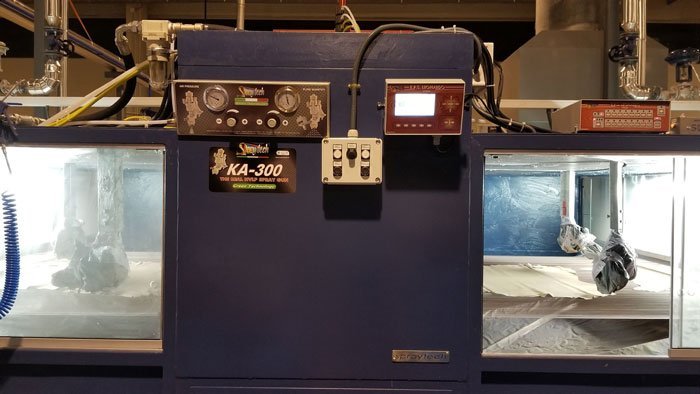
An example of REVAMPING MEDIUM, featuring the substitution of the Fly rotary carousel, rotary distributor, KA300 spray guns, RWS device and Leonardo Upgrading.
What are the benefits for the customers in choosing this option?
Besides improving the quality and efficiency of the machinery range, we guarantee cost reductions up to 50%. Obviously, SPRAYTECH will keep on producing and selling new systems, but, in this precise moment, when uncertainty is strong, targeted interventions on existing plants are very much appreciated, a less expensive solution, as the customer will be able to use the same kind of technology implemented on brand-new machines.
How will you explain this to Italian and foreign entrepreneurs?
We have put together a check-up list featuring ten questions that tanning entrepreneurs should ask themselves in order to better understand what can be improved and, above all, if they can save up by optimizing the use of their spraying plants. There is no doubt that the way to the future lies in the implementation of high-performance machinery, able to carry out different tasks, while keeping a keen eye on environmental safeguard and waste reduction. This questionnaire is devised to be a handbook not only for the enterprise’s owner, but also for the staff taking care of production and of maintenance operations, since the ultimate goal is the upgrading of the whole system.
Check-up to improve one’s spraying plant
1. Is my spraying plant efficient and safe?
2. Am I aware of the amount of product sprayed on leather and of the quantity dispersed in the painting booth and in the atmosphere?
3. Are the emissions measured in the booths compliant with law regulations?
4. Am I aware of the level of the spraying pressure?
5. Do guns spray only on leather? How many centimeters do I start to spray before and after on the leather perimeter?
6. How much does this waste cost me in terms of cleaning and disposal operations?
7. Am I satisfied with the finishing quality of the processed leather and how can I improve it?
8. How long does it take to perform colour change operations? How many times are these operations carried out in a day?
9. How long does a plant remain inactive during a day, a month and a year? And how much does this inefficiency cost me?
10. Are electrical consumption levels kept under control during the downtime phases? And if this does not happen, how can we reduce them?
Do you already have the answers to these questions, don’t you?
Of course. We are able to provide, for each single case, the best technological solution to the daily issues faced by tanners worldwide. The request for an onsite inspection, with our technicians, is the first step to a better production pattern, putting in the limelight pivotal themes such as cost reduction and environmental awareness, so as to safeguard our planet and become more competitive on an increasingly sophisticated market.
Can you give us an example of REVAMPING? Spraytech provides several REVAMPING options:
REVAMPING BASIC, featuring an intervention on the HVLP rotary distributor, on HVLP spray guns and on spray management electronics. Furthermore, we can replace the eight-arm rotary carousel with a new one equipped with 12, 16 or 24 arms;
REVAMPING MEDIUM that, in addition to the BASIC upgrading, it comprises also the addition of the RWS (Rapid Washing System) system, of flow regulators and the scale for consumption monitoring;
REVAMPING TOP that, besides the operations comprised in the MEDIUM package, it entails the implementation of the STS (Spraytech Time Saver) device, in order to speed up colour change operations, as well as of the LES (Leonardo Energy Saving) system, designed to save energy and increase efficiency.
Can you give us a demonstration of said economic benefits in terms of numbers and figures?
As evidenced by existing plants based in our customers’ companies, we are able to put in the limelight, for each type of REVAMPING, the following economic benefits:
With REVAMPING BASIC, it is possible to get up to a 30% reduction in the amount of product sprayed on leather, resulting in a marked drop in atmosphere emissions and in costs for booth cleaning operations:
As far as REVAMPING MEDIUM is concerned, in addition to the advantages ensured by the BASIC package, we register up to a 30% increase in productivity thanks to the fast washing of the plant’s circuits;
With regard to REVAMPING TOP, besides the MEDIUM benefits, there is also a reduction in energy consumption, amounting approximately to 40%, as well as further 40% growth in productivity thanks to the STS system.
To whom is the REVAMPING solution specifically addressed?
To the Italian and to the international market, without limits. However, in view of the fact that we are very well-known in the Arzignano district as we collaborate with over 90% of the local companies, and, due also to the fact that we provide maintenance services, we believe that we will receive more requests from abroad, where growth margins are remarkable. Bearing this objective in mind, in the last few months, we have strengthened our globalscale sales network, by hiring two other professionals in the role of export managers.
What are the most interesting foreign market?
We believe that the need to upgrade leather painting plants is a worldwide issue, especially in Asia, South America and Africa. Equally important is the fact that, after the installation phase, guaranteed by SPRAYTECH, the plant is eco-friendlier and less polluting. It is well-know that Italy fosters the strictest rules, so it is easy for us to show that the emissions are considerably lower compared to what happens abroad. www.spraytech.it