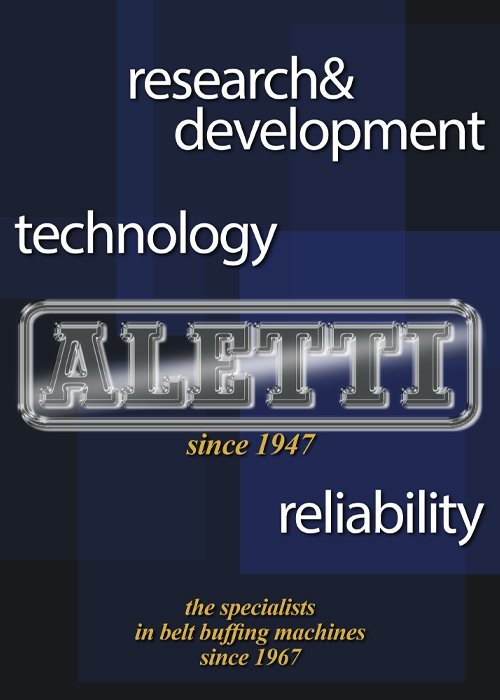
The Varese-based company Aletti is confirmed to be a leader thanks to its high-tech machinery, in great demand in the tanning sector, but also in the field of textiles and synthetic products.
From the left, Ezio, Carlo e Marco Aletti
“Surprisingly, 2020 was the best year of the last 15 years in terms of turnover.” These are the words of the engineer Marco Aletti, president and technical manager of ALETTI GIOVANNI & FIGLI, the company based in Varese boasting 74 years of experience in the tanning sector. “As a matter of fact, the performance achieved in 2020 – explains engineer Aletti – is the result of the work carried out in recent years aimed at enlarging our target markets. Despite the difficulties caused by the pandemic, which got the work and especially the installations abroad very complicated, we eventually achieved results that exceeded expectations. Over 90% of our turnover relates to belt buffing machines, which in the last ten years have been given priority for investments in research and development. In this sense we are at the forefront: in the last two years, in order to protect the most significant innovations from copying practices, that are sadly common in our sector, we have submitted four patent applications; two have already been granted and two are still under evaluation.
Are you worried about the situation arisen because of Covid-19? “The main problem is how long the global health emergency will last and how severe It will be, as it’s heavily affecting the global economy and all markets. Let’s say that in the medium term, thanks to the high markets diversification we carried on in recent years, I am confident, while I have some concern for 2021. In my opinion, this year we will suffer the consequences of the global economic crisis and the inevitable reduction of 2020 government support measures. We have been growing unceasingly for four consecutive years, with an average increase of 10-15% per year, despite the crisis in the tanning sector. We hope to grow further but, for 2021, we plan to stand still.
What company strategies have you implemented in recent years? “We have reduced in-house processing, relying on highly specialized suppliers, we have reduced the range of machines by focusing on belt buffers and we have considerably strengthened the design office, in order to offer different and customized solutions for the end user’s every need. The constant growth of the last few years is mainly due to the considerable investments in research and development that we have progressively increased in order to reach an average of over 8% of turnover: in the end we can say that it has been a winning strategy. An example to explain the change of course: until 2010, Aletti manufactured a ‘base’ belt buffing machine, customizable according to the different products to be processed; then we have gradually improved the range of buffers up to over five basic versions in ten working widths (from 800 to 3400 mm), which can be further customized, and that can be implanted in work lines complete with feeding supply systems, de-dusting systems and special accessories, always designed in-house.
Where is the market heading to? “The stalemate in many markets causes partial delays in the definition of some ongoing negotiations. It is essential to operate effectively on foreign markets. Aletti exports over 90% of its products all over the world, we are able to follow market developments, especially the Far East, which was the first to start growing again. The main problem that we’ll have to face and solve is the current travel limitations that cause delays in the installation of machines already delivered and push customers to hold off on new investments. Fortunately, thanks to developments related to digitization and remote assistance, Aletti is able to partially overcome these limitations. As far as we are concerned, we already have orders for the first four months of 2021 and commercial negotiations at an advanced stage to guarantee the company another six months of work. A year ago, that is, at the end of December 2019, we already had more than half of the turnover for the following year, given that the machinery of the lines for technical products are complex and require long design, building and testing times”.
Another of your flagships is the range of synthetic products buffers… “It is a sector that makes you think differently, because by contract the customer expects to have a fully reliable machine, able to work 24 hours a day with very high performance (up to 1500 rpm for the buffer): on our side we are able to guarantee a production speed of 18-20 meters per minute, while also ensuring very high precision and constant buffing quality. With such features, the entire package must be excellent, because every weakness in terms of reliability immediately stands out if the machinery is used within these timing. These machines represent excellence in the field of buffing and let us transfer our experience in the tanning sector, so to achieve a higher level of performance and reliability.”
Which model is the top of the range? “The ULTRABELT 3200 belt buffer (the number stands for the maximum width in millimeters of the buffer, ed.), which is registering excellent results, given that we are selling it to the most important international groups that process leather for furniture. It was a demanding project in terms of time and investment, since we had to go through constant improvements, innovations and fine-tuning both at the mechanical level and, given the high automation of the machine, at the software level. The array of available sizes has recently been extended and, for the ULTRABELT model, they now range from 2400 mm to 3400 mm. As for the markets, the largest turnover is achieved in China where our biggest customers are, namely world leaders in synthetic products. Asia and Europe are the most important outlets in the tanning field instead.
What other news have you recently launched on the market? “A range of buffers and de-dusting machines was created specifically for the ecofriendly materials, deriving from the recycling of leather, plastic, cork and other waste. Also, we have launched a special machine for high precision grinding, usable on any type of flexible material that requires a uniform thickness, ranging between +/- 0.01 mm. In the meantime, we are also solving the problems concerning the buffing of elastic products that require particular systems of feeding supply and to control the tightness of the product during the buffing phase. Before, it was possible to use buffers derived from the models used in the tannery, appropriately modified, but now the market requires special machines, featuring superior performance, automation and ease of use, even by non-specialized operators.
One last question: how is the technological aspect evolving? “As a matter of fact, there is a lot of work to do about the software, which in recent years has led us to thoroughly study the issues with our specialized technicians but also with outside specialists. Among the main features, linked to the Industry 4.0 investments of but also to cope with the problems of Covid-19, the possibility of intervening remotely and reliably providing remote assistance on every machine. By virtue of a full-blown evolution, we have equipped ourselves with a series of devices that communicate with each other; through this, we can extract from the machine a series of data that can be shared, for example, with different tanneries of the same group located in different parts of the world, in order to ensure the repeatability of the buffing parameters regardless of the production site. We are also designing new buffing technologies that we believe could set a new and superior standard in terms of quality and productivity, as happened in the past with the development of the belt buffer. That machine has been Aletti’s exclusive for fifty years and it is now a standard for the most important manufacturers of tannery machines. www.aletti.it