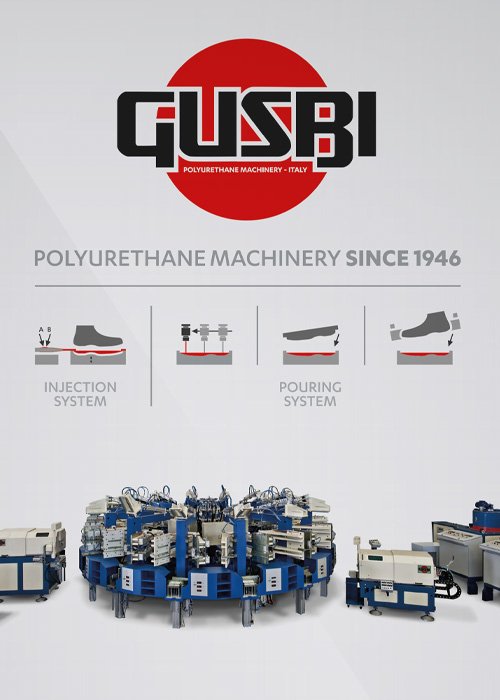
GUSBI, company based in Vigevano now relying on the third generation, stands out for its environmental awareness: a philosophy pursued since its establishment in 1946.
It was one of the first companies to get the “Green Label”, the tool set up by Assomac (that is, the National Association of Manufacturers of Footwear, Leathergoods and Tanning Technologies), a voluntary scheme that provides the end customer with useful information concerning the efficiency parametres and the environmental impact of the technologies produced. Based in Vigevano (Pavia province), GUSBI has turned environmental safeguard into a trademark, a philosophy pursued since it was established in 1946, right after the end of World War II, by Terenzio Bianchi and Emilio Gusberti – the latter in the ‘80s left his shares to the partner. Leader in the production of “turnkey” plants for polyurethane soles and footwear, GUSBI can now rely on the third generation of the family, as the granddaughter of the founder, Irene Bianchi, is successfully at the helm of the company.
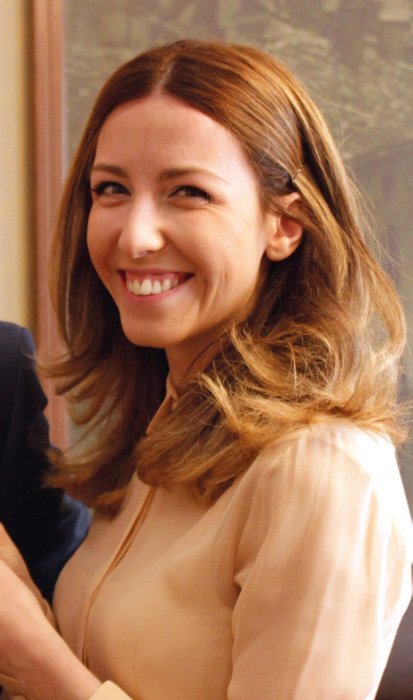
Irene Bianchi
“Since its foundation,” stated Irene, “GUSBI has been investing in the research and development of eco-friendly solutions, working hard day by day to foster a sustainable production. We are proud to say that we are direct protagonists of the circular economy, our machines allow customers to inject polyurethane, to recover waste and residuals, that are later broken down and injected again, continuously. For us, it’s nothing new: we have been aware of this technology for over twenty years, but only recently the majority of footwear companies has started looking for a sustainable method or acknowledging the pivotal role played by recycling. An increasingly pressing demand, especially in the fashion industry, where it is important for a brand to be sustainable and environmentally-friendly.”
How do you convey this message to the customers? Not everybody, especially abroad, is aware of this sustainability-oriented virtuous scheme. It is introduced to those who do not know anything about it, but, at the end of the day, it is just an option since it is not of common interest for all the markets: some acknowledge it in a positive way, others will get there when the time is right. In some countries, there are specific state investments and, therefore, entrepreneurs are definitely more motivated: in my opinion, this will become a topical issue in the upcoming future, as the line has been drawn everywhere by now. Obviously, the final decision lies in the customer’s hands: we always recommend this solution, given that we already own a technology designed to blend polyurethane with cork ad the latter can be replaced with a recycled material. In this sense, we do not have to upgrade the machine, as it is perfectly suitable for a fully eco-sustainable policy. The Green Label certification is not a mere tag, but it is the meaning of a “mission” we strongly believe in. More and more companies are eager to get that. A customer of ours who purchased the plants 10-15 years ago, called of his own accord an external consultant have them certified.
Traditionally, the so-called “carousels” consume a lot of energy. Are your plants “energy-intensive”? Energy-saving policies should be implemented right at the source, as the main issue is usually related to the equipment. Our company designs and manufactures plants, each one of them assembled by using components purchased from the best multinational corporations that, thanks to sophisticated, expensive energysaving departments, invest a lot of resources in the supplying of accessories conceived to reduce consumption. In other words, the best way to provide a lowconsumption machine is to employ components specifically devised to ensure that. We are qualified, we know a lot about this topic, about “carbon footprint”, that is, the system that certifies the consumption in terms of CO2 impact and emissions, certified by the RINA institute in Genoa.
Can you give us an example of sustainability in the production cycle? An interesting instance concerns the washing of the machinery’s head. In the past, solvents were usually used, that is, chemical agents that, especially in a limited production area, result in an unpleasant smell and are breathed in by the employees. Therefore, something hazardous both for the environment and for the workers’ health. We have developed a new process that consists in the use of warm water at 80°, so as to completely avoid chemicals. There is nothing better that water, since it does not pollute and, at the same, it helps reduce solvents’ costs. This is a project we have been carrying on for quite some time, we have always thought about it and now we want to include it in the plant’s standard system.
What kind of advantages does it entail to choose a “green” policy? Several, as confirmed by numbers and figures. And the strategies to deal with the “green” issue are varied as well: for example, when a customer must choose whether distributing the release agent with a robot or by hand, we have noticed that, in the second case, the operator tends to use a large amount of product in order to be sure. There is also a quality-related problem: if said agent is over distributed, it might lead to an aggressive polishing or resulting in stains on the sole. On the other hand, the robot, specifically designed to “follow” the cavity in the mould by using a precise number of grams, distributes the substance more efficiently, thus ensuring not only higher quality standards, but also a drop in consumptions and costs. Companies based abroad, where labour costs are lower, often prefer to perform said operation manually, but several are changing strategy. Some customers are opposed to the idea of implementing anthropomorphic or collaborative robots, but, when we manage to convince them, the results are truly favourable. www.gusbi.com